Strategic Utilization of Tie Wire for Weight Balancing.
For a wide array of projects, tie wire, also called binding wire, may be used for its flexibility. Applications include joining fencing, supports, and other objects together. In the construction and landscaping industries, this type of wire has become an essential component for creating structures. Additionally, tie wire can come in various lengths and strengths to suit many requirements.
When it comes to tying, the weight of the tie wire must be taken into account to properly select the right product. Various elements contribute to the heaviness of tie wire, such as swage, material, and size. The thickness of the wire will determine its diameter which will establish its weight. Likewise, different materials like steel, aluminum, and copper also come with varying weights.
When it comes to wire, length matters. The more stretched out a single strand is, the heavier the weight. This heaviness is usually measured in pounds per thousand – lb/K, with the larger the numeral, usually indicating heavier material. So, for a twelve-gauge wire measuring 1000 feet, the weight would equate to a hefty 16 lbs/K.
Finding the optimal tie wire for the task at hand is dependent on its weight. Lighter wires may be unable to take up the load and stress that comes with certain purposes, whereas heavier wires are more resistant to breaking or bending, adept in conditions of extensive utilization. Notably, heaviness indicates plus points when it comes to load bearing capability; for instance, a heavier wire can manage more heft than a lightweight option.
Looking at weight is undoubtedly essential when searching for the appropriate option for your project. However, it is just as essential to consider the length of the wire when making this selection. In other words, longer lengths naturally will be bulkier than more abbreviated lengths, so it is paramount to determine what length of wire you need for the intent of the task. Longer lengths are often needed when constructing fences, stakes, etc., while more modest lengths are generally better for more minuscule jobs or structures.
For any job, selecting the right wire is essential, and there are a few key characteristics to consider, such as the wire’s weight, material, and length. Choosing the right tie wire weight for the task at hand ensures that a sturdy and dependable link is created.
For most construction jobs, tie wire is paramount to success. This material is used to combine components, normally as a short-term binding option. These wires usually consist of steel or aluminum and come in an assortment of gauges that are dependent on the task at hand. When selecting the right wire for a job, heavy consideration must be given to the weight of the wire – one of the most important factors in the decision process.
When it comes to determining the optimal weight of tie wire, we use a measurement called lb/Mft, which stands for pounds per thousand feet. This is a quick and convenient way of weighing a massive quantity of wire in one go. Although heavier wire will usually be stronger and longer lasting, it may end up being more costly in the long run, so it’s essential to select the right weight for your specific application.
Tying wire is available in multiple weights: 16 lb/Mft, 18 lb/Mft, and 20 lb/Mft. The lightest of the three, 16 lb/Mft, is well-suited for tying small bundles of plants and shrubs or more delicate materials like fabric. When a bit more staying power is needed, 18 lb/Mft is the more practical option and is often used to keep pieces of fencing together or to bind steel rebar during construction. For maximum strength, 20 lb/Mft is best for tasks like tying together heavy steel beams.
When selecting a tie wire for an application, you must think about the weight and durability of the material. Steel tie wire is the toughest and can last for years, but it is also the priciest. Meanwhile, aluminum is quite light and budget-friendly, but weaker. Weighing up the two options demands that you consider both the overall weight of the wire and its strength. That’s the key to pinpointing the right choice.
When choosing the right tie wire, the weight and material of the wire, as well as its size, corrosion resistance, and availability must be taken into account. Bigger wires have an advantage in that they can handle heavier loads whereas corrosion resistant kinds would more likely last longer. Furthermore, it is wise to be aware of the wire’s availability in the area so that it can be easily procured when needed.
Selecting the right tie wire for a given task is of critical importance; one must consider various factors such as weight, size, material, and corrosion-resistance in order to make an optimal choice. Typically, heavier wires boast greater strength and longevity, yet assessing their availability is just as crucial. Many components go into picking the most suitable tie wire; determining if it fits the job requires thoughtfulness and detail.
Related Product
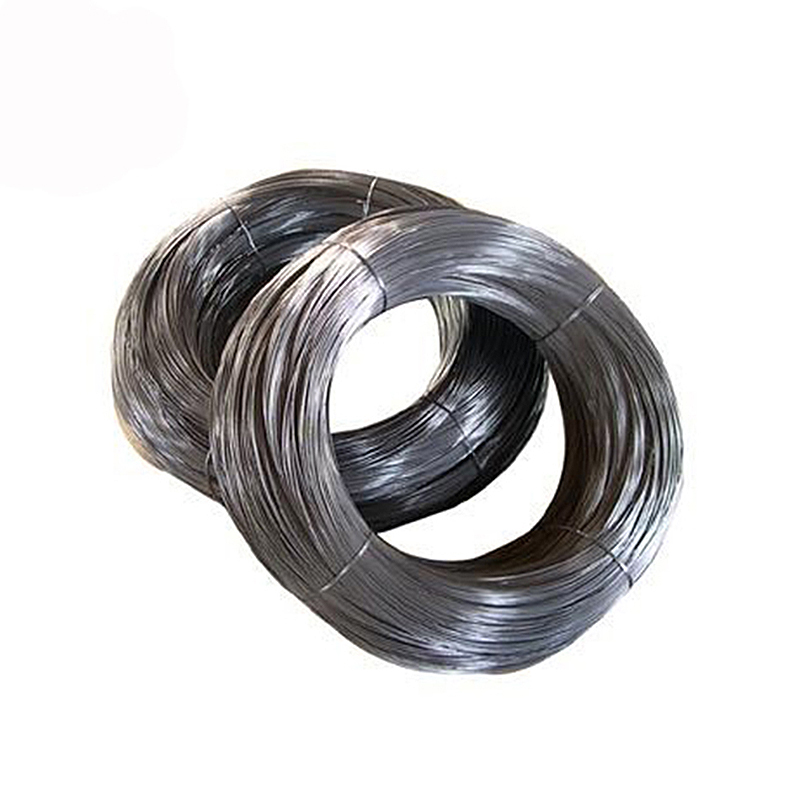
Galvanized Wire
Product information: Product Name Galvanized Wire Package 5kgs/roll, pp film inside and hassian cloth outside or pp woven bag outside 25kgs/roll, pp film inside and hassian […]
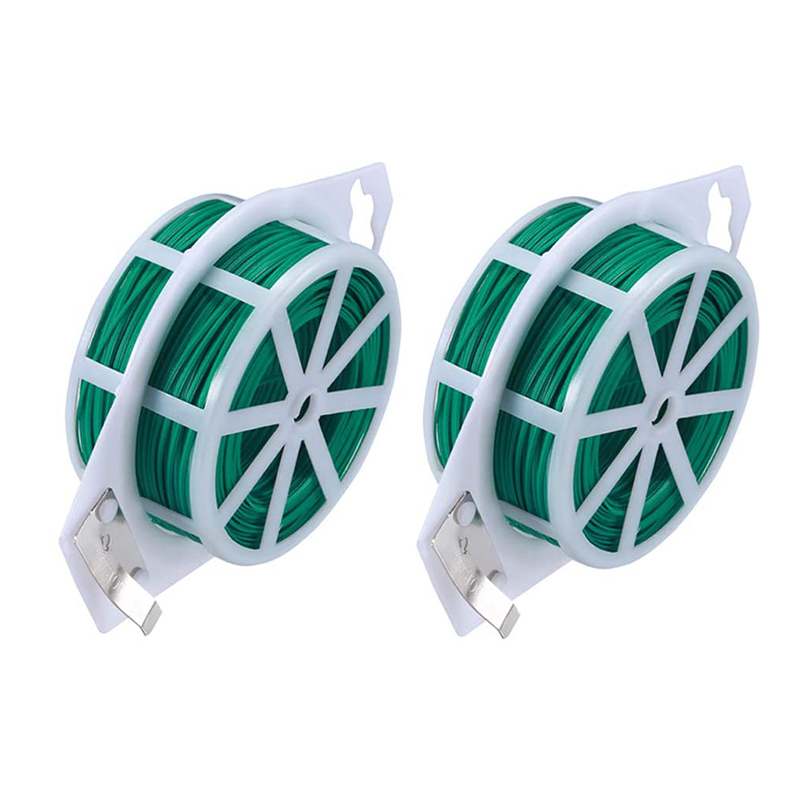
Garden Wire
Product information: The garden shingling is made of pvc plastic and high-quality galvanized iron wire, which is 3 to 4 times faster than any material, and the buckle is loose, the […]
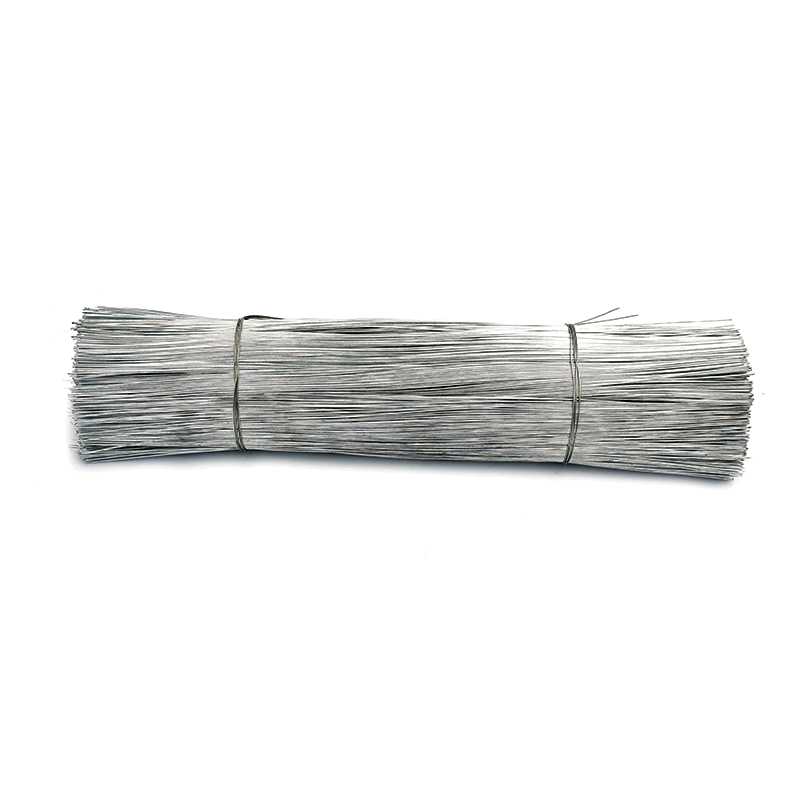
Cutting Wire
Product Description: Product Name Cutting Wire Zinc Coating 30-70g Place of Origin Chinese mainland Tensile Strength 33-50kg/mm2 Material Electro galvanizedHot dipped galvan […]
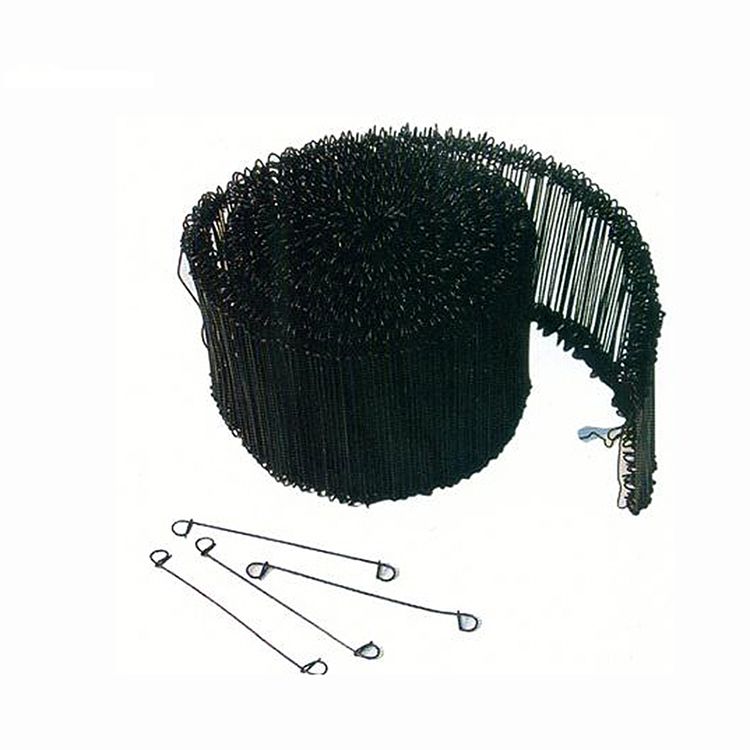
Double Loop Tie Wire
Double loop tie wire material Product Information: Wire diam. 0.5mm—2.0mm Finishes Black Annealed. Galvanized Annealed, Coppered, PVC coated, Stainless steel Wire gauge BWG6 […]
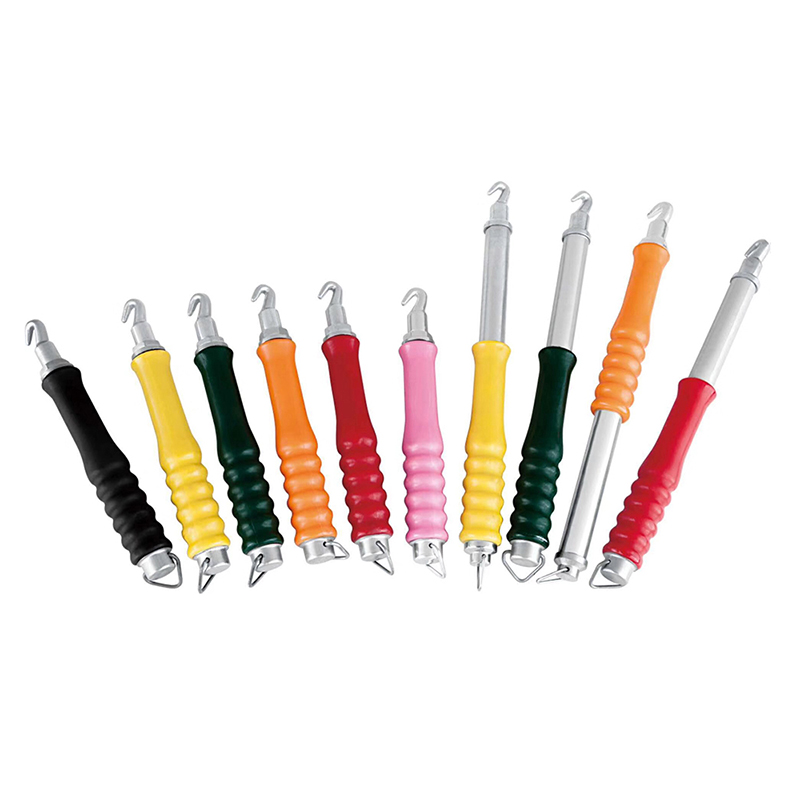
Twister Tool
Handle Twister tool,plastic handle: Weight: 0.4kg Color: Black, blue,yellow ,red etc Material: Carbon Steel Plastic Handle Wire Tie / Tying Hook Tool Twister Wooden Handle […]
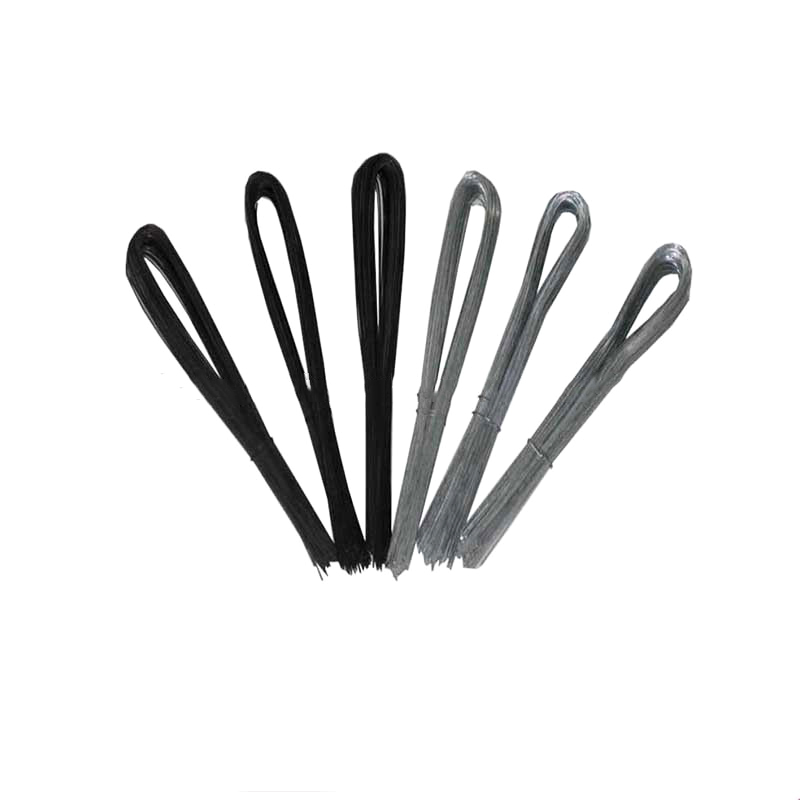
U Type Wire
Product information: Product Name Scaffolding Packing Galvanized Tie Wire Cuttings U Type Binding Wire Material Electro galvanized,hot dipped galvanized,black annealed,PVC coated W […]
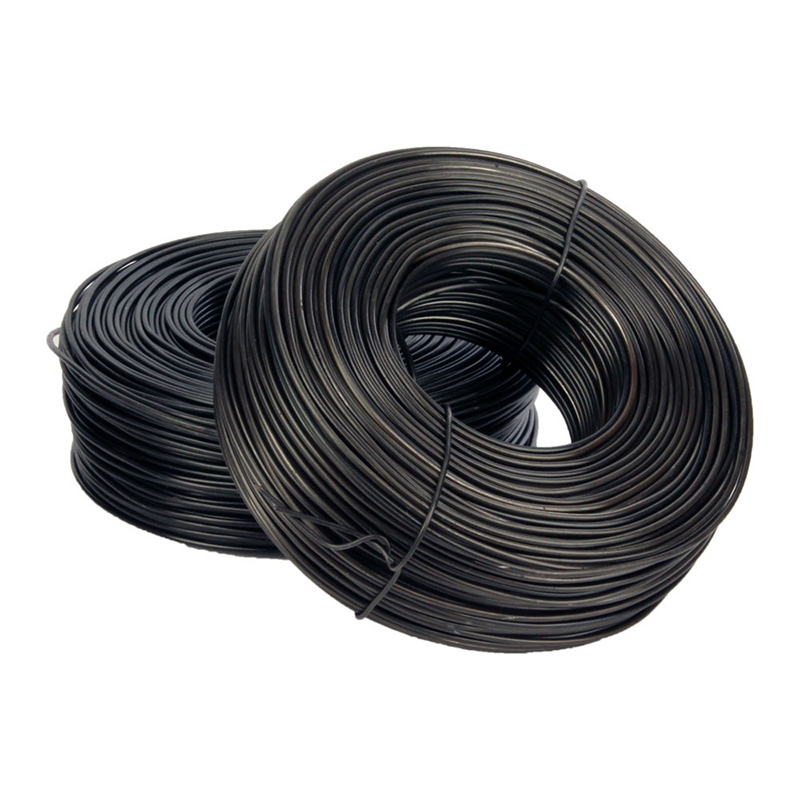
Tie Wire
Production Process of rebar tie wire : Steel rod coil — Wire Drawing — Wire Annealing–Rust Removing–Acid Washing– Boiling– Drying– Zinc Feeding– Wire Coiling. Wires Type 1.Galvaniz […]
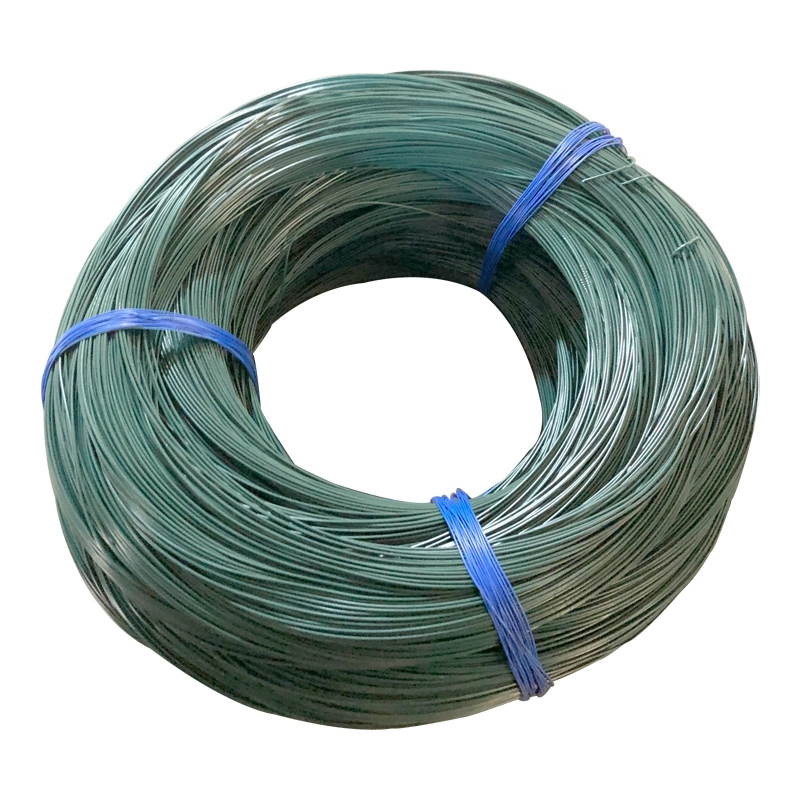
PVC Coated Wire
PVC coated wire, also called plastic coated wire, after high temperature dissolution cooled solid PVC particles uniformly wrapped in high-quality black iron wire and galvanized wi […]
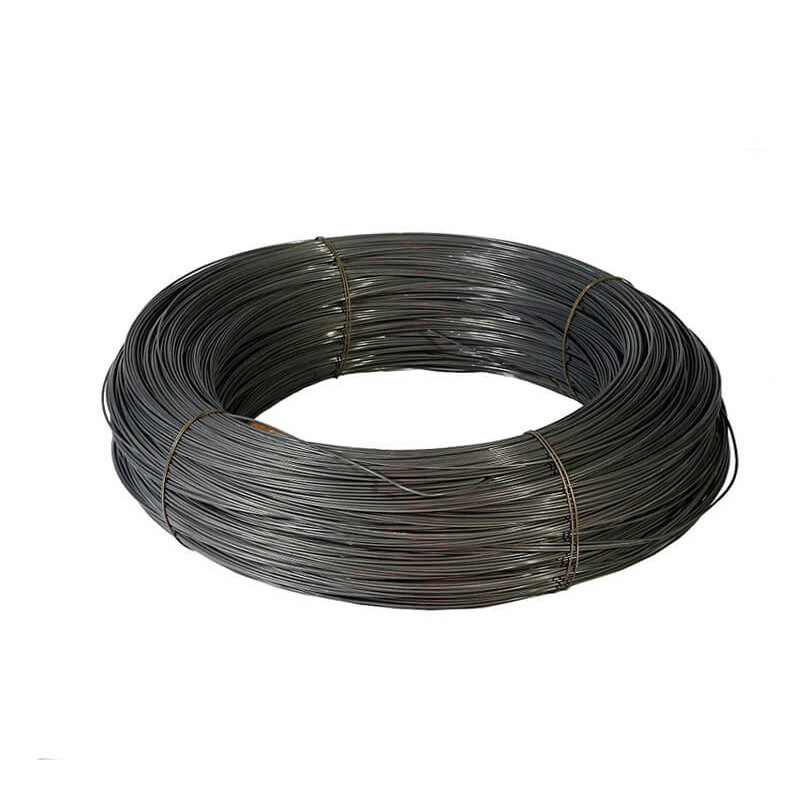
Black Annealed Wire
Product Description: Product name Black Annealed Wire MOQ: No Material Q195,Q235 Delivery time: 20days after payment Surface annealed or as your request Payment terms: T/T,L/C We […]
Post time: 2023-08-07