Wire tying has myriad uses ranging from construction and industrial applications to horticultural and textile-based ones. Tie wires, otherwise referred to as lacing wires, are employed to join disparate objects together in a firm, immutable connection. This can encompass materials such as rebar and wire mesh but is also practiced in the fastening of plants within the horticulture sector or even fabrics in the textiles industry. By passing the wire through the desired objects then twisting, a strength build-up is achieved which culminates in a sturdy assemblage.
To guard against rust and support greater strength and sturdiness, tie wires are frequently fashioned from galvanized steel. This material is fashioned from a steel wire coated in zinc. It comes in fully assorted sizes in both thick and thin diameters, as well as lengths, which can be trimmed to fit whatever project you are working on.
Construction materials such as rebar can be kept firmly secured with the employment of tie wires. These versatile wires are weaved through the steel bar and create a durable and reliable connection that strengthens the concrete, making it more dependable when used to construct the likes of buildings and other industrial facilities.
Fastening wires are used to affix wire mesh firmly in order to make the installation more durable and ensure greater structural support. Additionally, they may be used for keeping metal fabrications like grates and grills in place and ensuring they do not slip or loosen over time.
From securing plants in the horticulture industry to affixing fabrics in the textile field, tie wires are incredibly utilitarian tools. The simplicity of the product is what allows it to be used across various industries: a wire is inserted through the material, its ends twisted together and voila –a reliable hold is provided.
A spectrum of gauges and lengths can be chosen from when selecting tie wires. Cutting them to size is an option for specialized applications, and they are presented as both galvanized and non-galvanized versions. Galvanized tie wires in particular provide enhanced durability and rust-resistance, making them the preferred choice for outdoor and aquatic applications.
Construction and industrial applications rely heavily on the use of tie wires for a variety of purposes. Used to secure items like rebar, wire mesh, metals and fabrics, they come in different diameters and lengths easily adjustable. Galvanized ties are perfect for outdoor use due to their rust resistance, otherwise known as non-galvanized, but the preferred form is usually galvanized when setting up projects in the marine environment. Tie wires remain an invaluable resource for the construction and industrial world, allowing for one’s project to secure a sturdy and dependable grip.
Metal wiring can be employed to stitch together a variety of objects, from furniture and fences to intricate machinery components. Fastening these pieces with metal ties requires little skill but there are multiple approaches that can be taken depending on the desired outcome.
Having the appropriate tools is paramount when it comes to succesfully tying metal wire. Specifically, you’ll need a pair of pliers and some wire cutters, with the former for grasping and bending the wire and the latter for trimming it down to size. It is essential to make sure that both the wire cutters and pliers are of excellent quality, as this will ensure that the wire remains intact while being shaped.
Once the proper tools are attained, the following question presents itself: how should the metal wire be fastened? When it comes to tying wire, there are three common techniques: the regular knot, the loop knot, and the figure-eight knot. The simplest and most routine of these is the conventional knot, and is useful for minor fastening jobs such as enclosing a fence or securing pieces of furniture. For heavier objects, a loop knot is preferable to provide additional stability. Finally, when seeking an especially strong bond, the figure-eight knot is the recommended approach.
Grasp the wire with the pliers, allowing around four inches of slack, and form a loop. Then, carefully turn the ends in the opposite direction before snuggling them together to create a tight knot.
Gripping the wire firmly with the pliers, begin by sculpting it into a loop. Next, switch directions and spin the ends until they rotate in the opposite direction. To secure the knot, loop the wire around itself and tie it. Lastly, twist the ends together until they are tightly bound.
Grasping the wire with the pliers, twist it into a loop and then turn the ends in the opposite direction. Secure these by weaving the wire around itself, then fasten them together in an intricate figure-eight design until they are tightly bound. This is how you tie a figure-eight knot.
After the connection has been established, it is essential to make sure that the cord remains secure. The tension of the wire should not be too light or too snug; otherwise, it can lead to either slackening or snapping. Furthermore, take care to keep the loop centered around what it is connected to; it will ascertain balanced security.
Crafting knots with metal wire is an essential element in many assembly and repair actions. Even though it is quite an uncomplicated activity, using the right equipment and adhering to the proper instructions are key to assure that the ties hold firmly. With careful practice, anyone can learn the skill of properly securing projects together.
Related Product
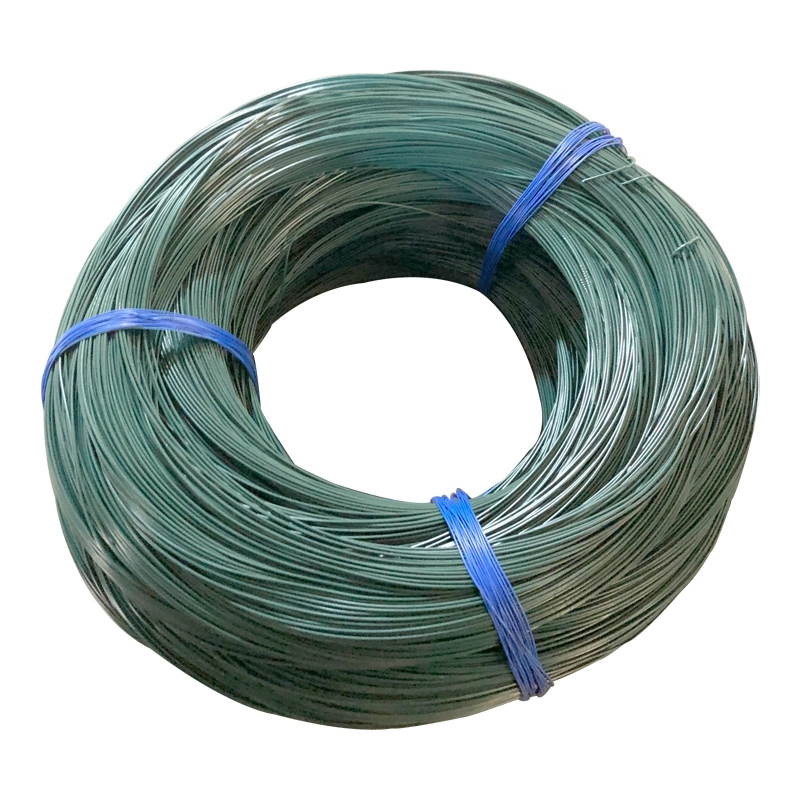
PVC Coated Wire
PVC coated wire, also called plastic coated wire, after high temperature dissolution cooled solid PVC particles uniformly wrapped in high-quality black iron wire and galvanized wi […]
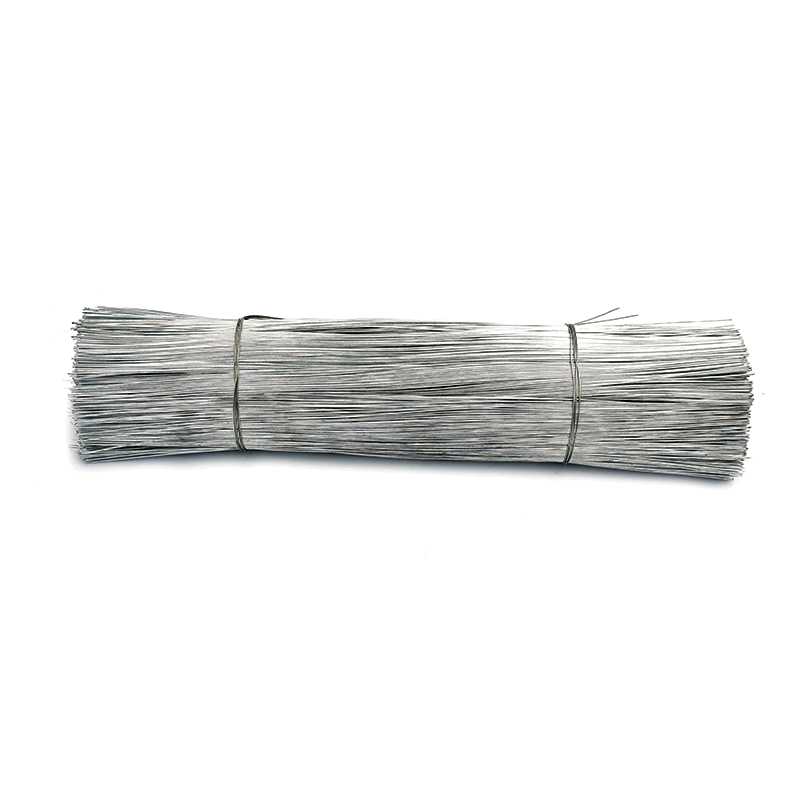
Cutting Wire
Product Description: Product Name Cutting Wire Zinc Coating 30-70g Place of Origin Chinese mainland Tensile Strength 33-50kg/mm2 Material Electro galvanizedHot dipped galvan […]
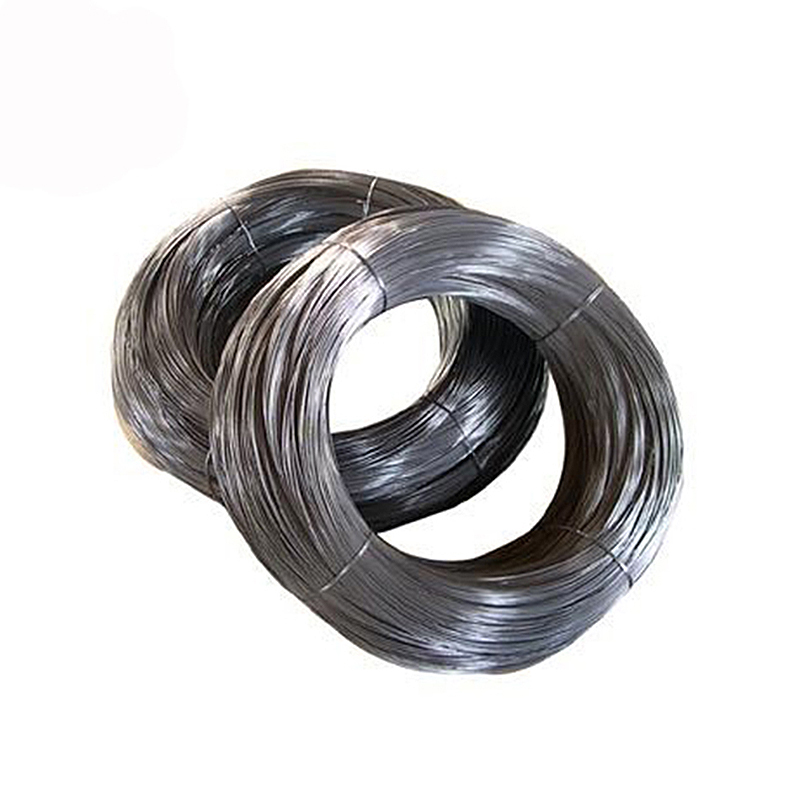
Galvanized Wire
Product information: Product Name Galvanized Wire Package 5kgs/roll, pp film inside and hassian cloth outside or pp woven bag outside 25kgs/roll, pp film inside and hassian […]
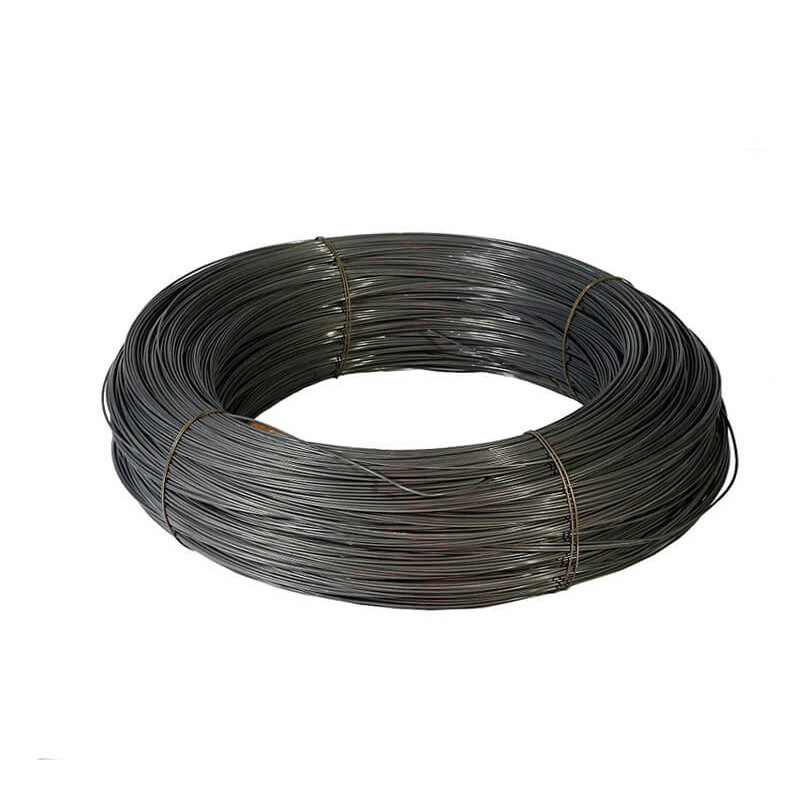
Black Annealed Wire
Product Description: Product name Black Annealed Wire MOQ: No Material Q195,Q235 Delivery time: 20days after payment Surface annealed or as your request Payment terms: T/T,L/C We […]
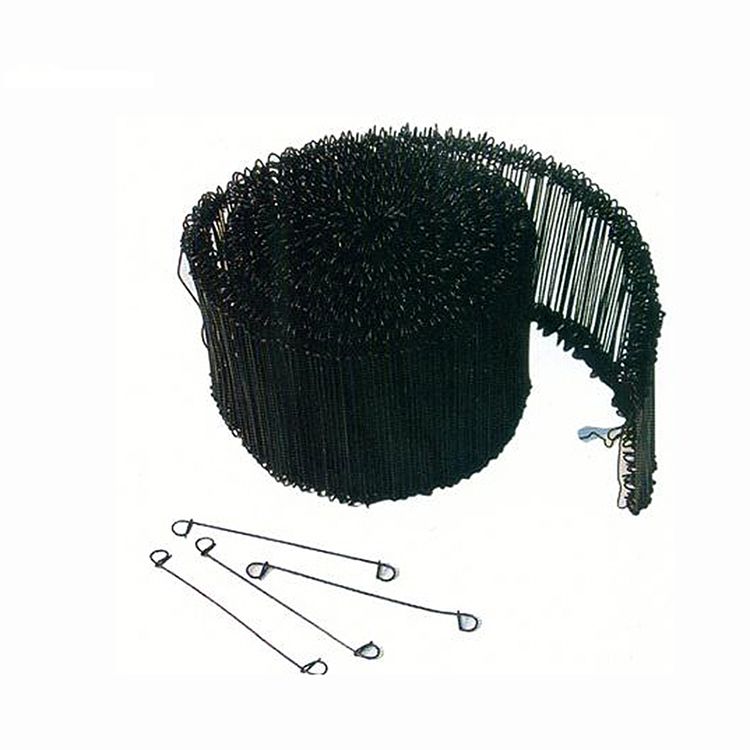
Double Loop Tie Wire
Double loop tie wire material Product Information: Wire diam. 0.5mm—2.0mm Finishes Black Annealed. Galvanized Annealed, Coppered, PVC coated, Stainless steel Wire gauge BWG6 […]
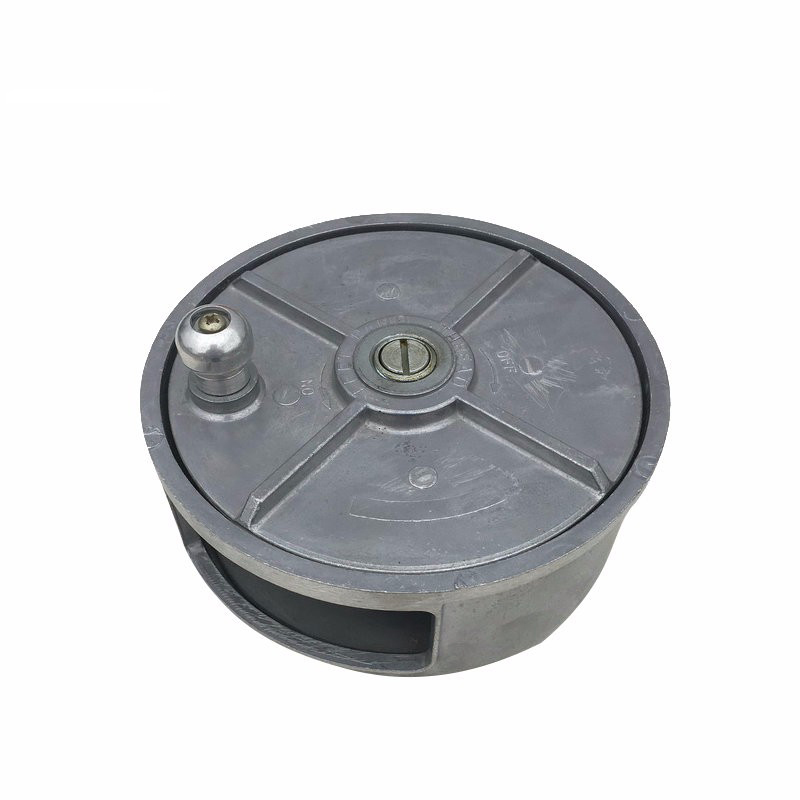
Reel Wire Tool
Product information: Specification of Aluminum Tie Wire Reel Material Plastic & Aluminum Weight 1.95LBS Application Binding Wire MOQ 1000pcs Sample Free Package 5PCS/CARTON &nb […]
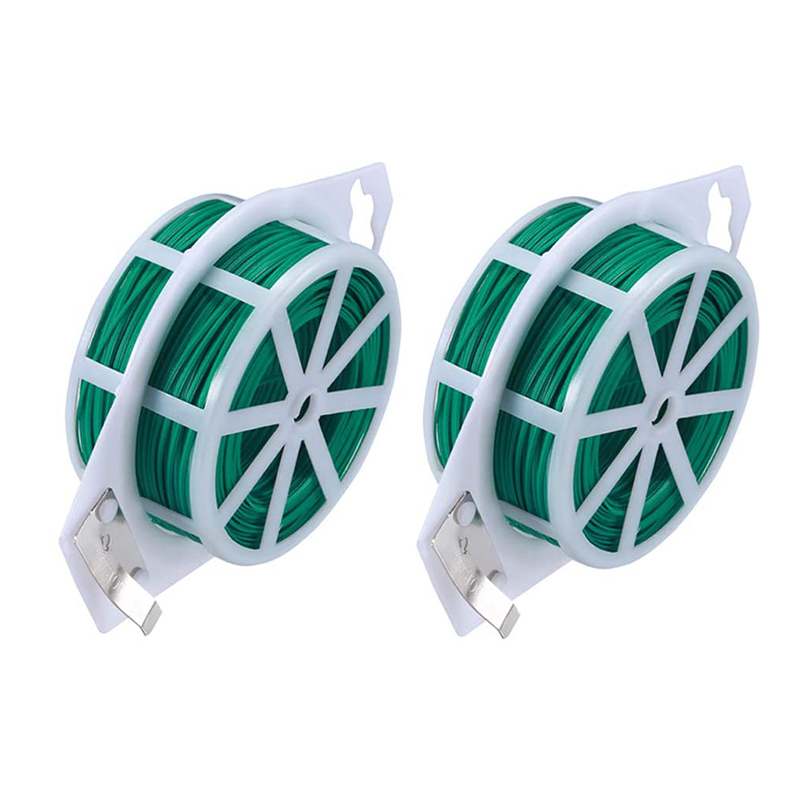
Garden Wire
Product information: The garden shingling is made of pvc plastic and high-quality galvanized iron wire, which is 3 to 4 times faster than any material, and the buckle is loose, the […]
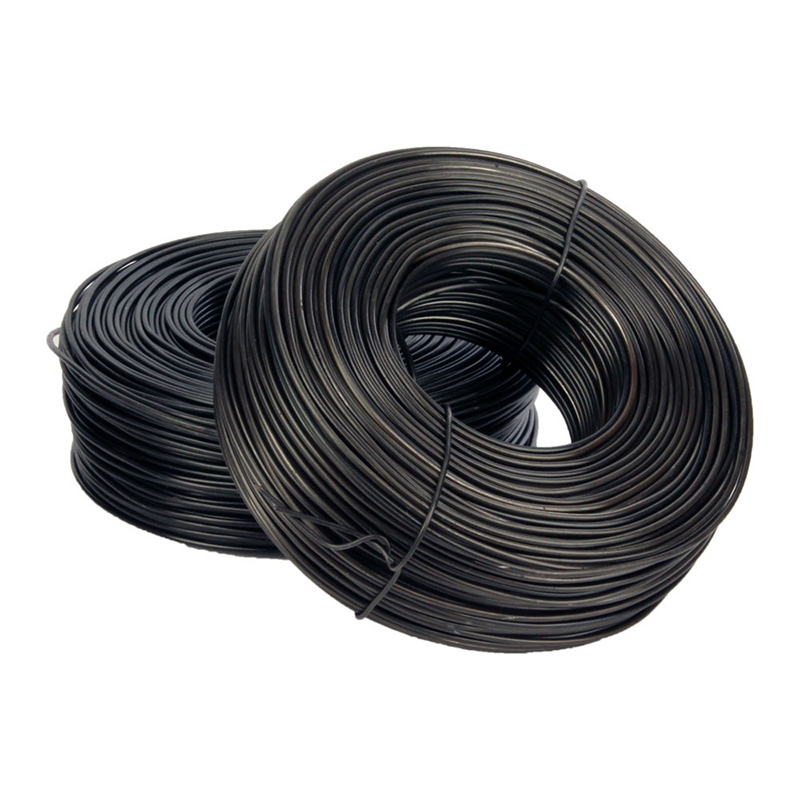
Tie Wire
Production Process of rebar tie wire : Steel rod coil — Wire Drawing — Wire Annealing–Rust Removing–Acid Washing– Boiling– Drying– Zinc Feeding– Wire Coiling. Wires Type 1.Galvaniz […]
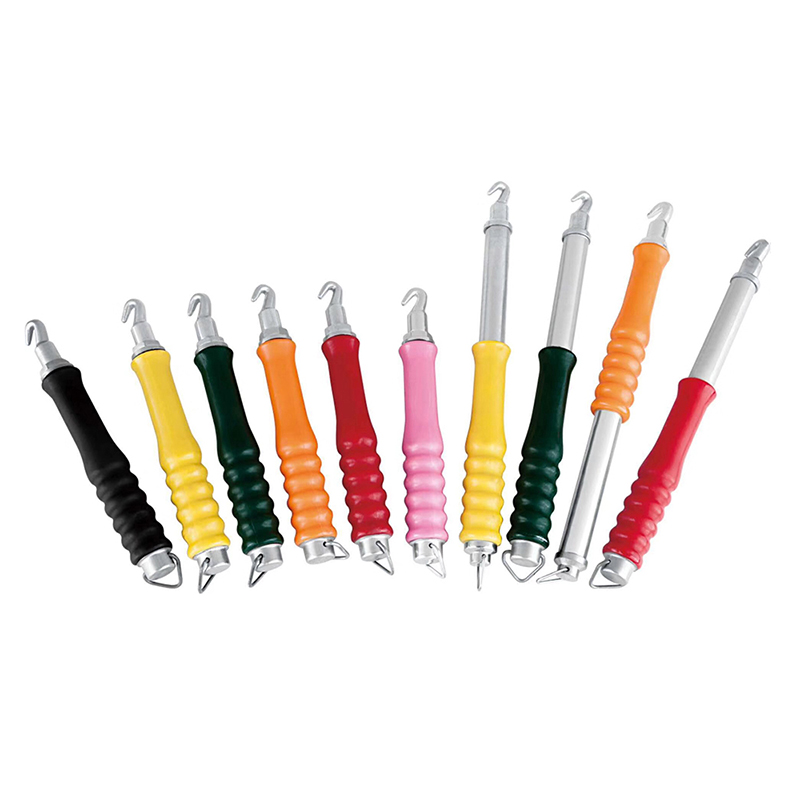
Twister Tool
Handle Twister tool,plastic handle: Weight: 0.4kg Color: Black, blue,yellow ,red etc Material: Carbon Steel Plastic Handle Wire Tie / Tying Hook Tool Twister Wooden Handle […]
Post time: 2023-08-02