Loads on vehicles and trailers need to be securely locked – that’s where tie and lashing wires come in. But that’s not all they can do – they can also be utilized to construct makeshift fencing or secure objects in a building site. There are two major types of these wires: high-tensile and galvanized. High-tensile wires are fashioned from tough steel, granting them significant resilience, whereas galvanized ones are bathed in a zinc coating for maximum corrosion and rust resistance.
Various tie and lashing wire options are available, ranging from inch (6.4 mm) to 3/8 inch (9.5 mm), and from 50 feet (15.2 m) to a whopping 250 feet (76.2 m) in length. The most frequently encountered gauges are 1/4 inch, 5/16 inch, and 3/8 inch while the most popular lengths are 50, 100, and 250 feet respectively.
When securing a load or ensuring that the wire won’t slip from its place, tie and lashing wires come in handy. To apply proper tension to the wire, wire tensioners are used, coming in various shapes and sizes – the two most common being ratchet tensioners and cam tensioners. With these tensioners, the wire can remain tight and unyielding.
To make sure you always have the right tool for the job, you can rely on tie and lashing wires in tandem with wire cutters to get the job done. There are various sizes and kinds of cutters available, such as ratchet and rotary cutters, to snip the wire when it’s no longer needed.
When it comes to tie and lashing wires, steel is often the first choice. Boasting strength and durability, as well as being corrosion-resistant makes it an ideal material for this purpose. When deciding upon the type of steel to choose for a tying and lashing wire, two common grades typically present themselves – high carbon steel and stainless steel. High carbon steel is the strongest of the two options, making it the best choice for heavy-duty applications. However, if you’re looking for something more resistant to corrosion, stainless steel’s your go-to; it is less strong than its counterpart but offers greater protection from its environment.
For applications that call for tie and lashing wires, there are a variety of available colors to choose from. The two most popular alternatives are black and galvanized. Black wires, for the most part, are suitable only for short-term solutions due to their lack of rust and corrosion resistance. On the other hand, galvanized wires have an additional layer of zinc applied, which protects against any potential deterioration.
Related Product
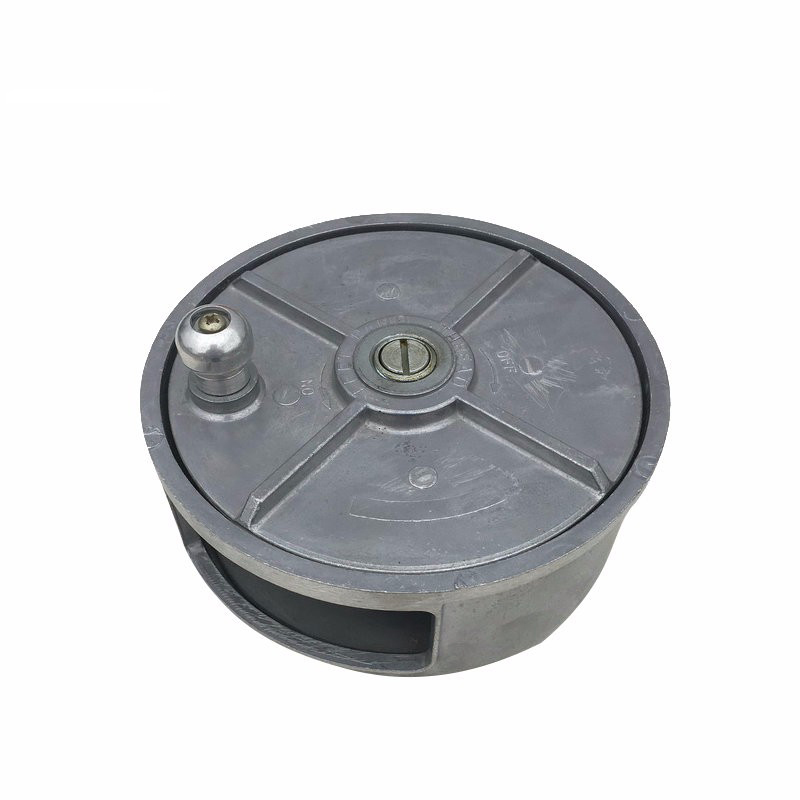
Reel Wire Tool
Product information: Specification of Aluminum Tie Wire Reel Material Plastic & Aluminum Weight 1.95LBS Application Binding Wire MOQ 1000pcs Sample Free Package 5PCS/CARTON &nb […]
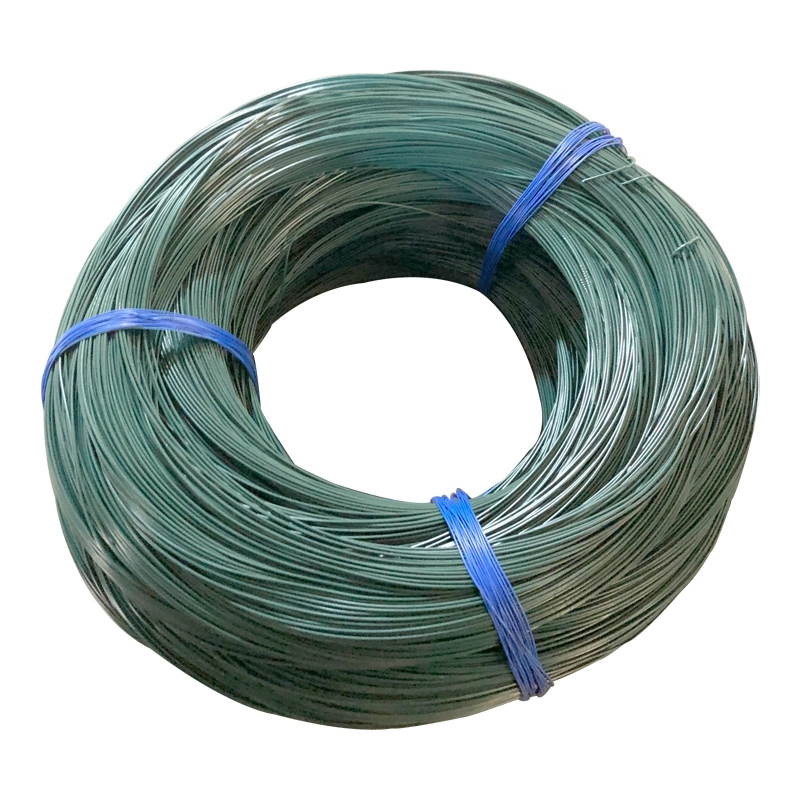
PVC Coated Wire
PVC coated wire, also called plastic coated wire, after high temperature dissolution cooled solid PVC particles uniformly wrapped in high-quality black iron wire and galvanized wi […]
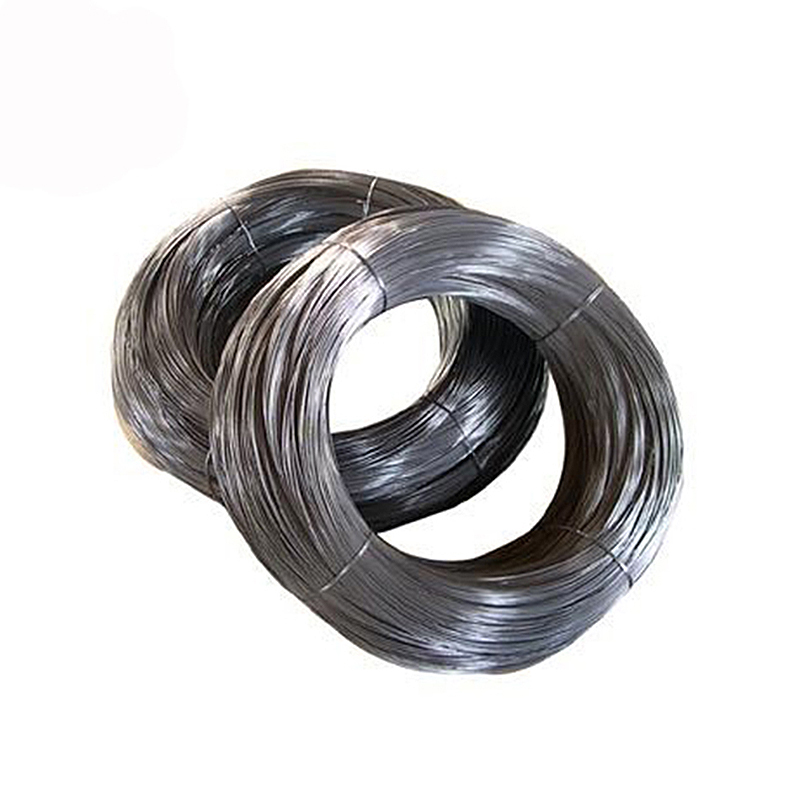
Galvanized Wire
Product information: Product Name Galvanized Wire Package 5kgs/roll, pp film inside and hassian cloth outside or pp woven bag outside 25kgs/roll, pp film inside and hassian […]
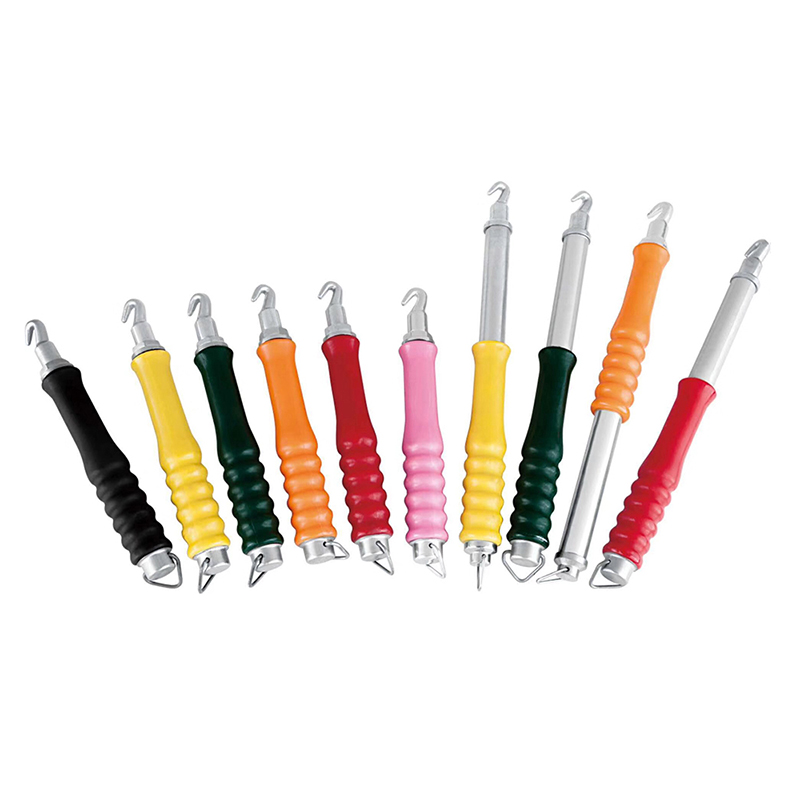
Twister Tool
Handle Twister tool,plastic handle: Weight: 0.4kg Color: Black, blue,yellow ,red etc Material: Carbon Steel Plastic Handle Wire Tie / Tying Hook Tool Twister Wooden Handle […]
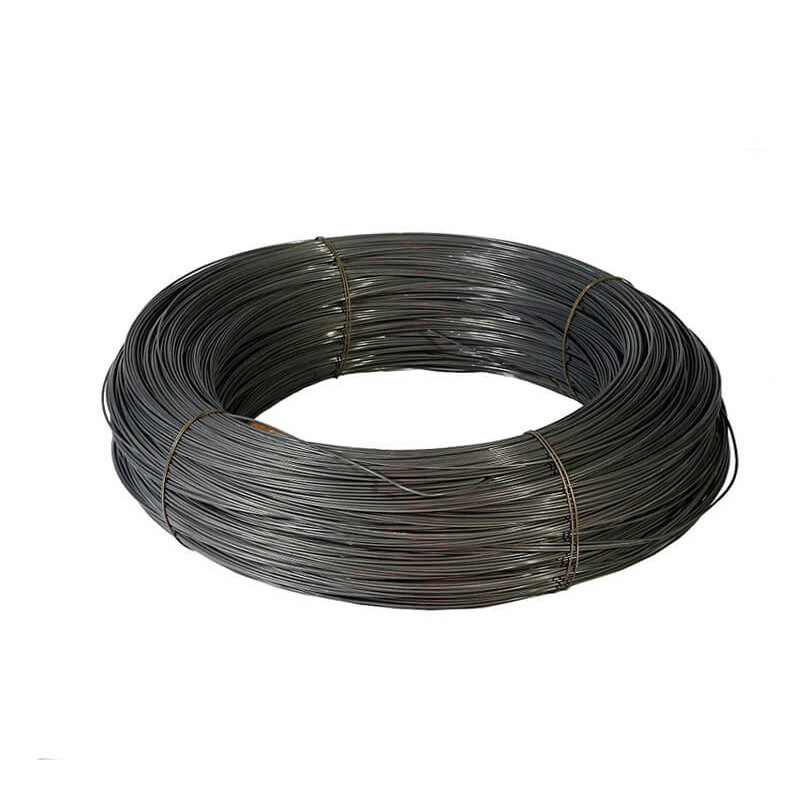
Black Annealed Wire
Product Description: Product name Black Annealed Wire MOQ: No Material Q195,Q235 Delivery time: 20days after payment Surface annealed or as your request Payment terms: T/T,L/C We […]
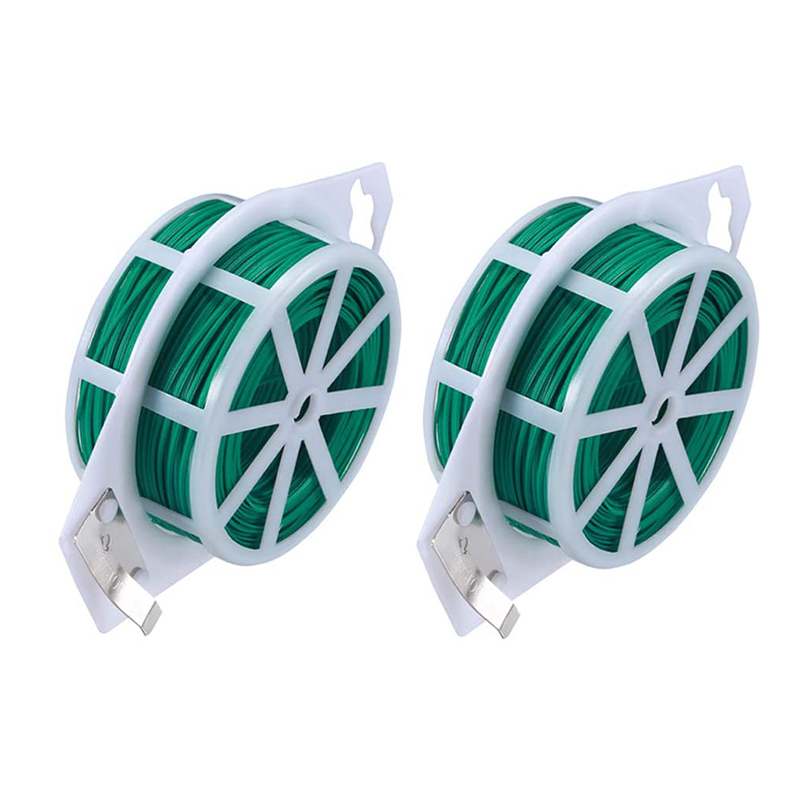
Garden Wire
Product information: The garden shingling is made of pvc plastic and high-quality galvanized iron wire, which is 3 to 4 times faster than any material, and the buckle is loose, the […]
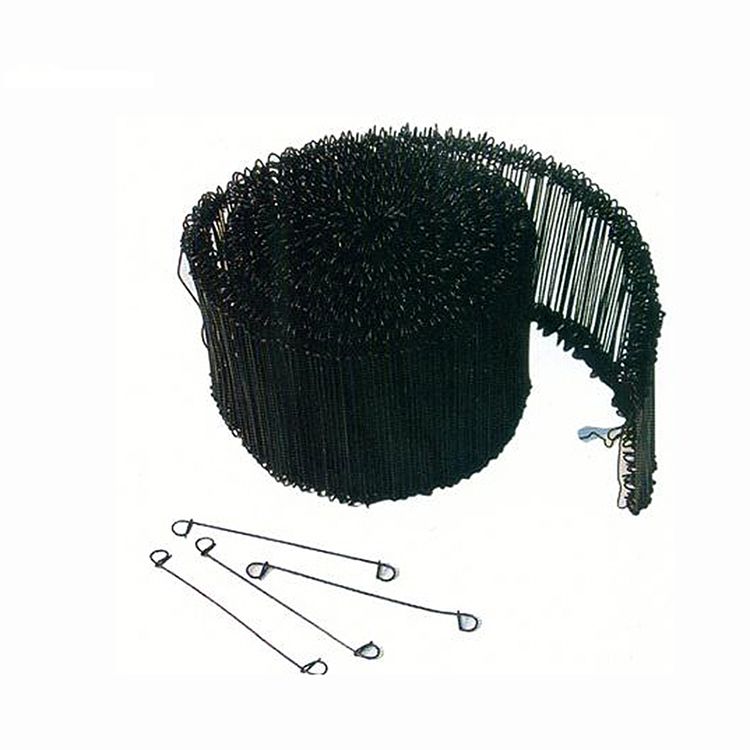
Double Loop Tie Wire
Double loop tie wire material Product Information: Wire diam. 0.5mm—2.0mm Finishes Black Annealed. Galvanized Annealed, Coppered, PVC coated, Stainless steel Wire gauge BWG6 […]
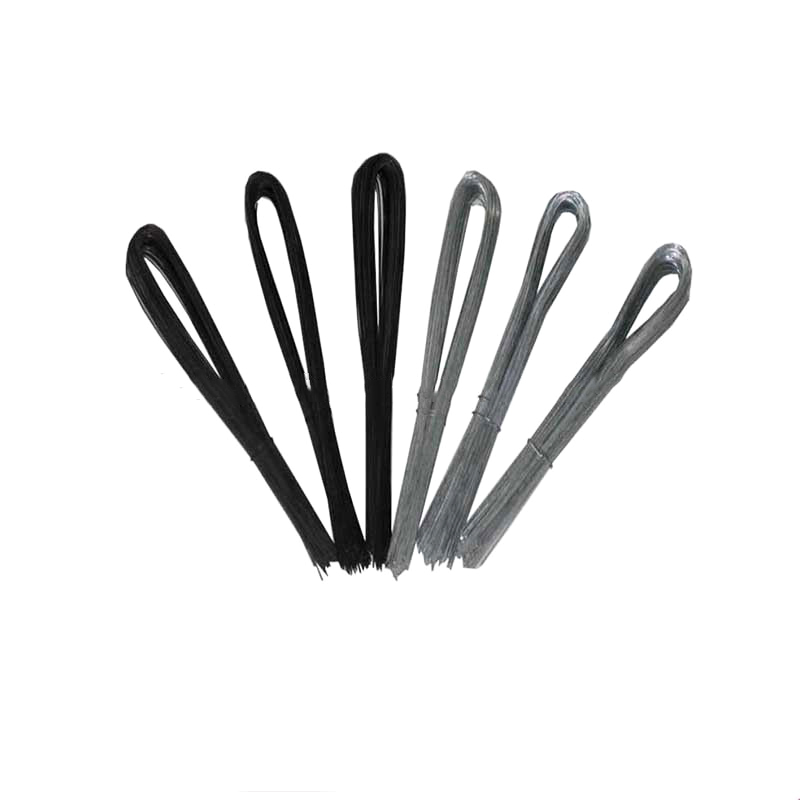
U Type Wire
Product information: Product Name Scaffolding Packing Galvanized Tie Wire Cuttings U Type Binding Wire Material Electro galvanized,hot dipped galvanized,black annealed,PVC coated W […]
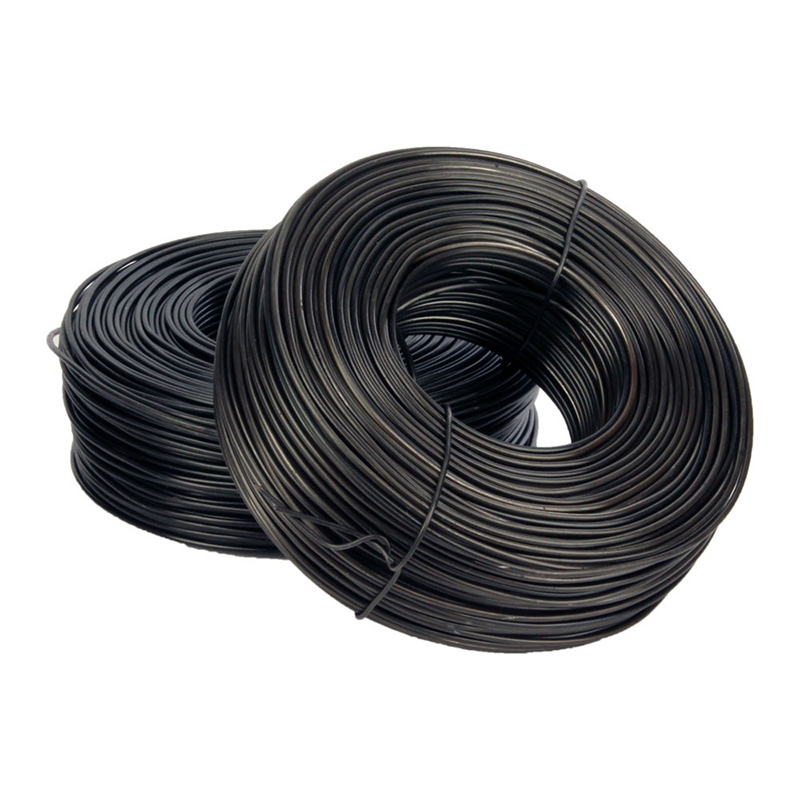
Tie Wire
Production Process of rebar tie wire : Steel rod coil — Wire Drawing — Wire Annealing–Rust Removing–Acid Washing– Boiling– Drying– Zinc Feeding– Wire Coiling. Wires Type 1.Galvaniz […]
Post time: 2023-06-27