An anti-corrosive layer of zinc coats galvanized tie wire to provide stability and durability. From large-scale structural reinforcement to smaller-sized projects like binding and fencing, this versatile wire is widely used in the construction industry. Moreover, it serves plenty of practical purposes such as tie wire applications for added security.
A coating of zinc applied to tie wire, a process known as galvanizing, is generally achieved through hot-dip galvanization. This method submerges the wire in a bath of molten zinc which bonds with the metal, forming a protective layer. Electroplating is also an alternative option for conducting this practice.
Galvanized tie wire proves to be an exceptional choice for outdoor applications; its impervious zinc coating ensures it is resistant to rust and other forms of corrosion, allowing the wire to endure in even the most inhospitable of environments. Additionally, its greater flexibility than uncoated wire makes it easier to manipulate and work with.
When handling galvanized tie wire, one must equip themselves with a pair of gloves to safeguard against any potential harm the zinc can cause. Also, due to the sharpness of the wire, one has to be extra careful and take extra precaution not to be injured. Additionally, if not stored in a dry place, the zinc coating on the wire may be prone to peeling off. So, proper storage is essential for its long-lasting usage.
When shopping for an enduring, dependable wire, galvanized tie wire may be the perfect solution. Its reliable protection against oxidation, combined with its economical price point and wide availability, make it a worthwhile investment.
Related Product
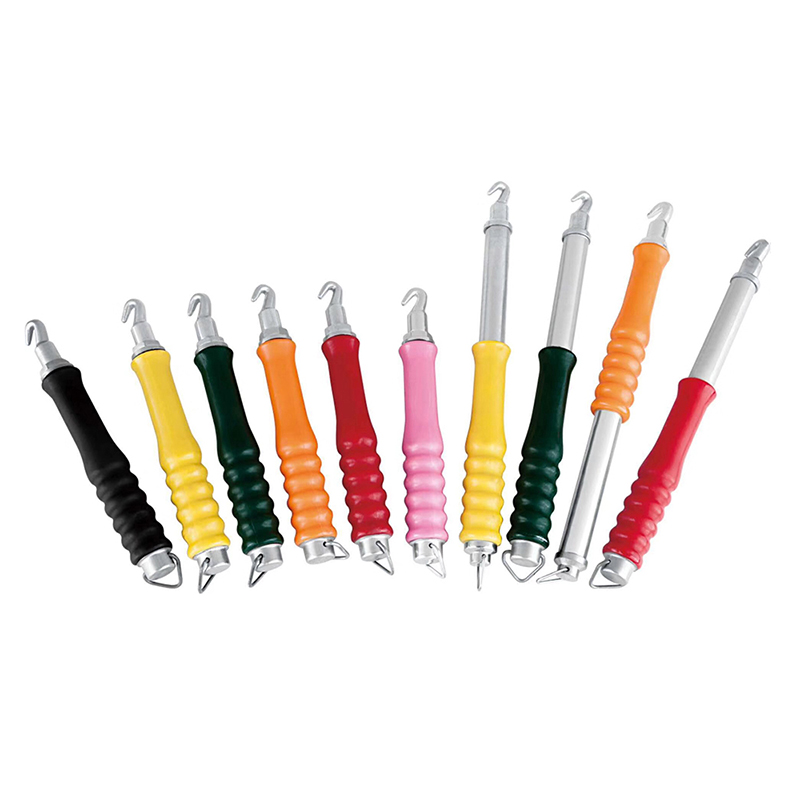
Twister Tool
Handle Twister tool,plastic handle: Weight: 0.4kg Color: Black, blue,yellow ,red etc Material: Carbon Steel Plastic Handle Wire Tie / Tying Hook Tool Twister Wooden Handle […]
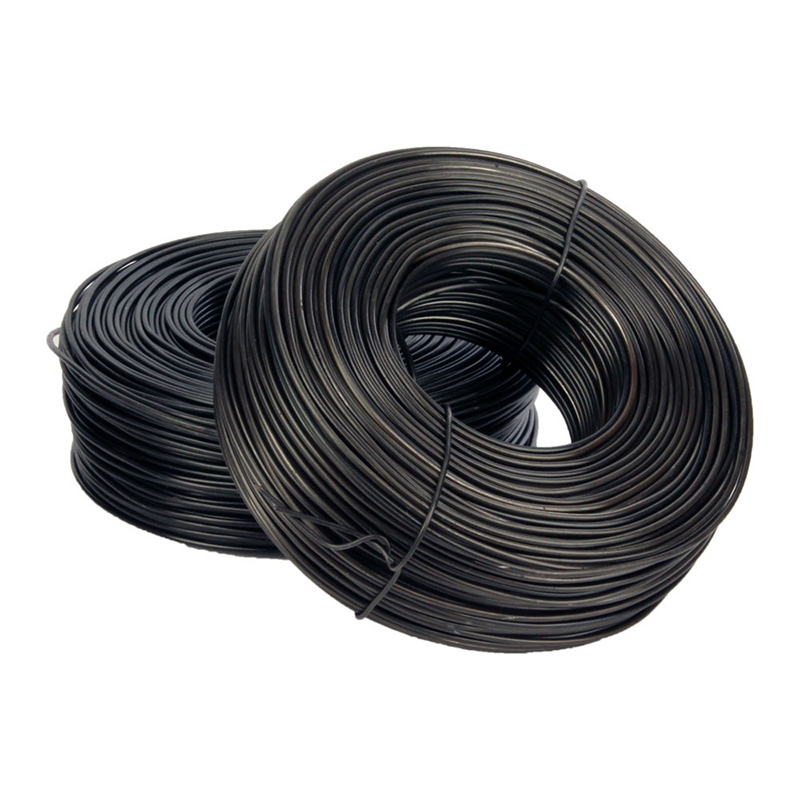
Tie Wire
Production Process of rebar tie wire : Steel rod coil — Wire Drawing — Wire Annealing–Rust Removing–Acid Washing– Boiling– Drying– Zinc Feeding– Wire Coiling. Wires Type 1.Galvaniz […]
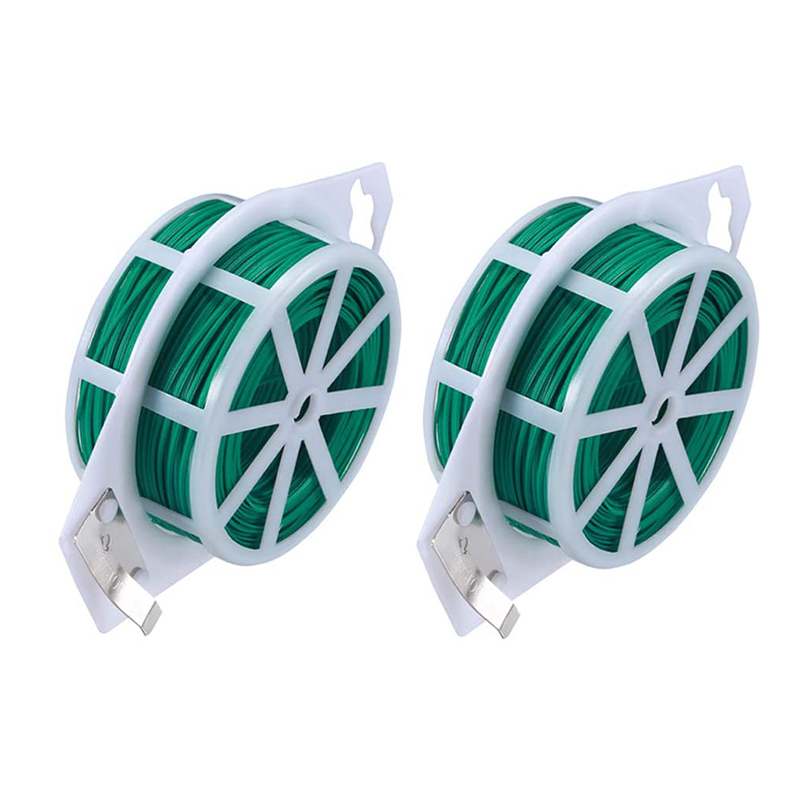
Garden Wire
Product information: The garden shingling is made of pvc plastic and high-quality galvanized iron wire, which is 3 to 4 times faster than any material, and the buckle is loose, the […]
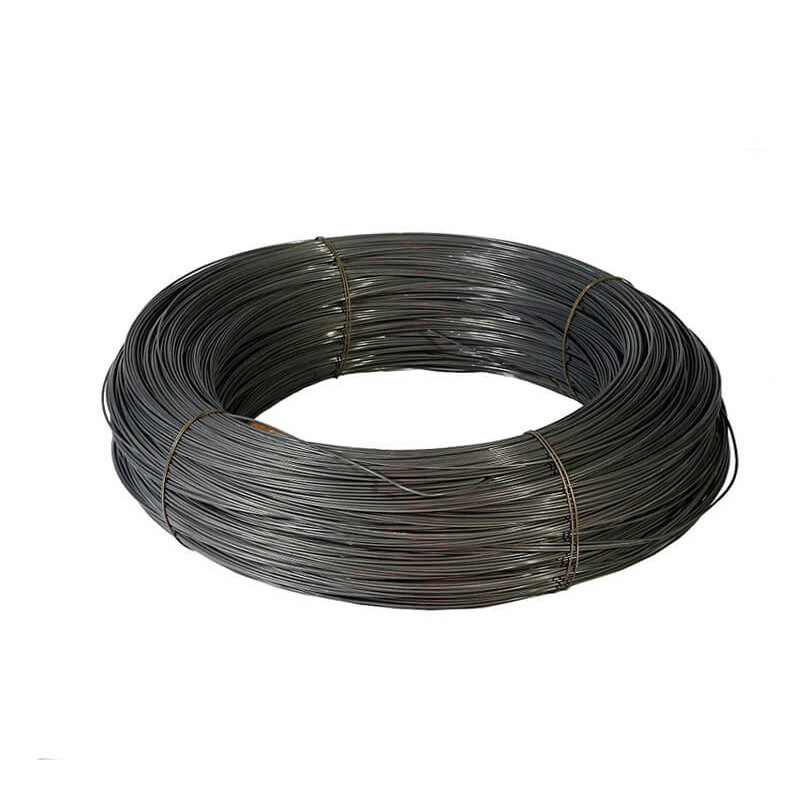
Black Annealed Wire
Product Description: Product name Black Annealed Wire MOQ: No Material Q195,Q235 Delivery time: 20days after payment Surface annealed or as your request Payment terms: T/T,L/C We […]
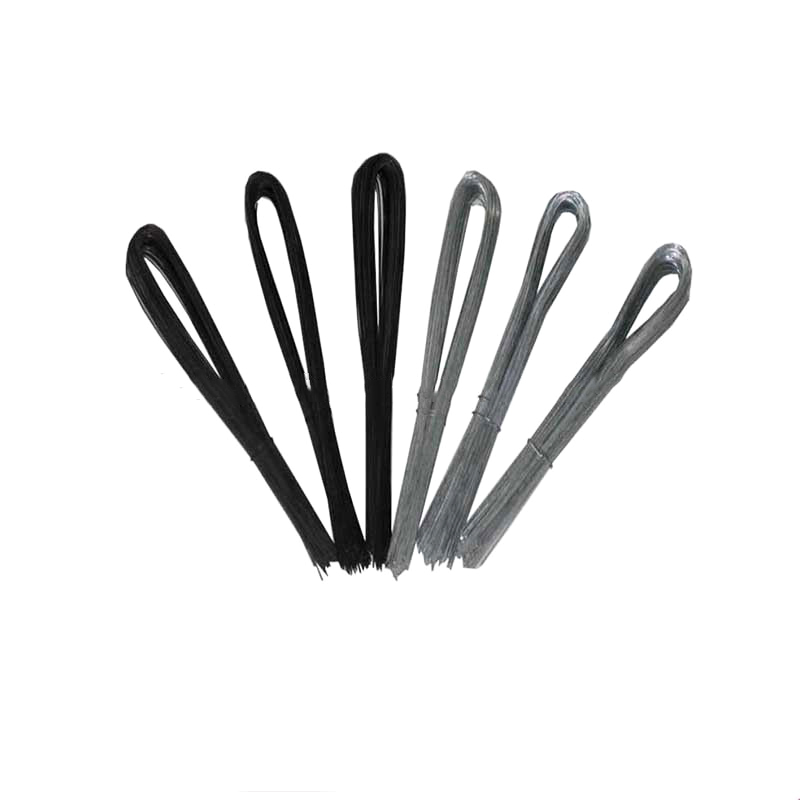
U Type Wire
Product information: Product Name Scaffolding Packing Galvanized Tie Wire Cuttings U Type Binding Wire Material Electro galvanized,hot dipped galvanized,black annealed,PVC coated W […]
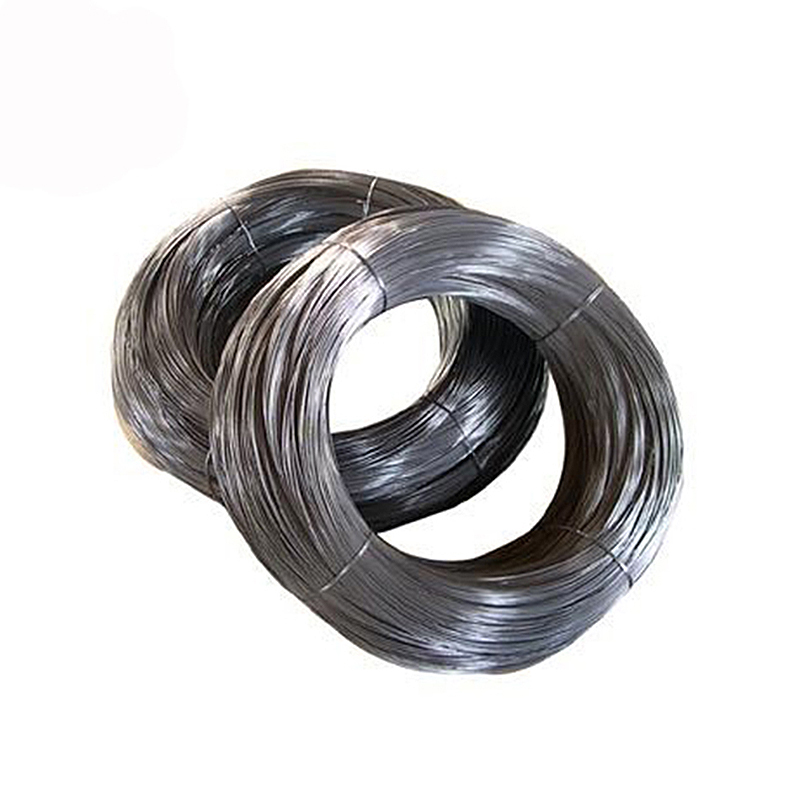
Galvanized Wire
Product information: Product Name Galvanized Wire Package 5kgs/roll, pp film inside and hassian cloth outside or pp woven bag outside 25kgs/roll, pp film inside and hassian […]
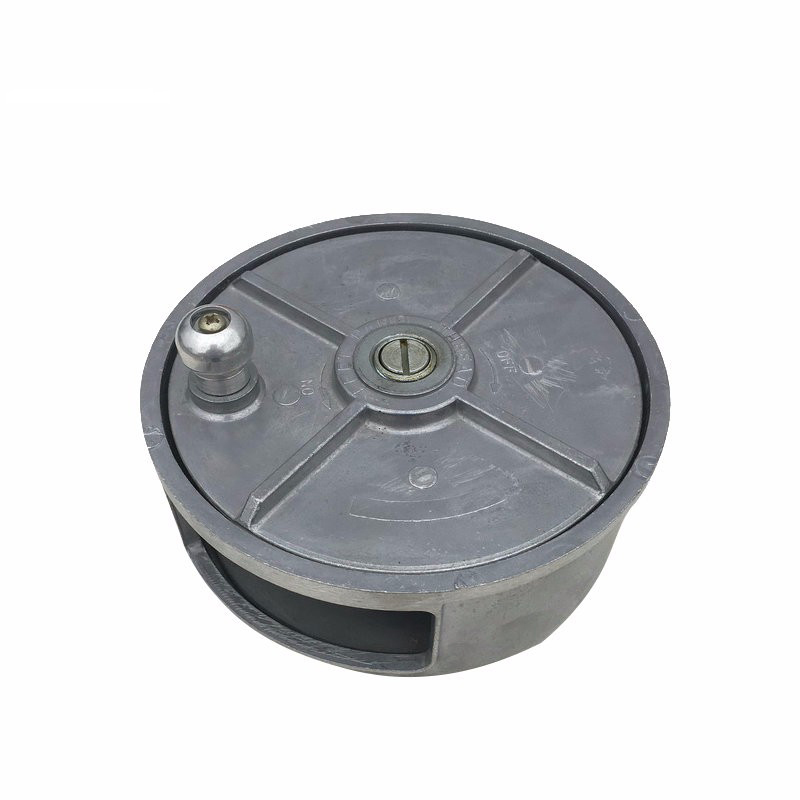
Reel Wire Tool
Product information: Specification of Aluminum Tie Wire Reel Material Plastic & Aluminum Weight 1.95LBS Application Binding Wire MOQ 1000pcs Sample Free Package 5PCS/CARTON &nb […]
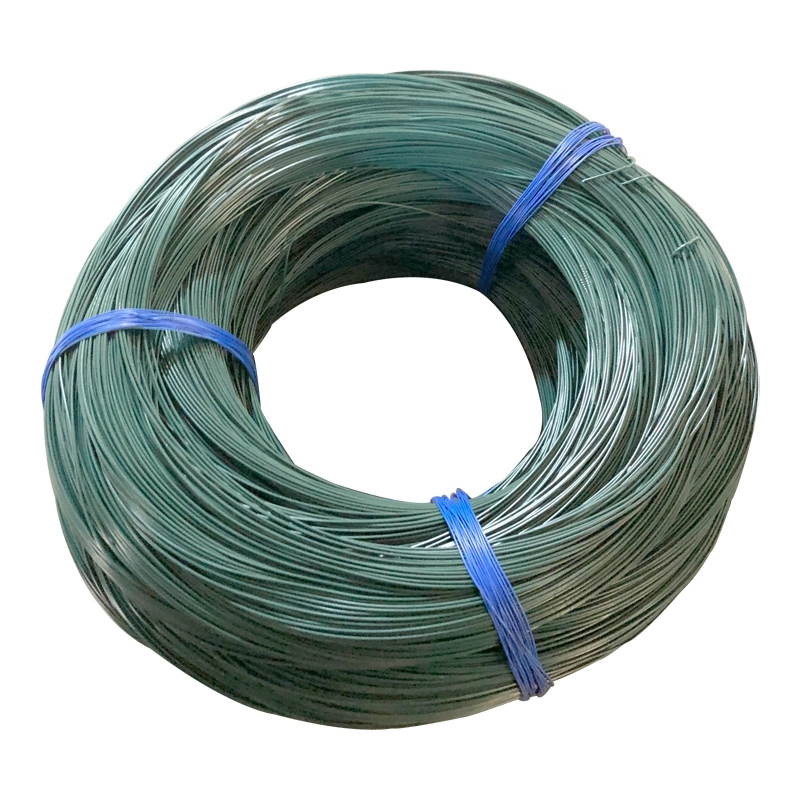
PVC Coated Wire
PVC coated wire, also called plastic coated wire, after high temperature dissolution cooled solid PVC particles uniformly wrapped in high-quality black iron wire and galvanized wi […]
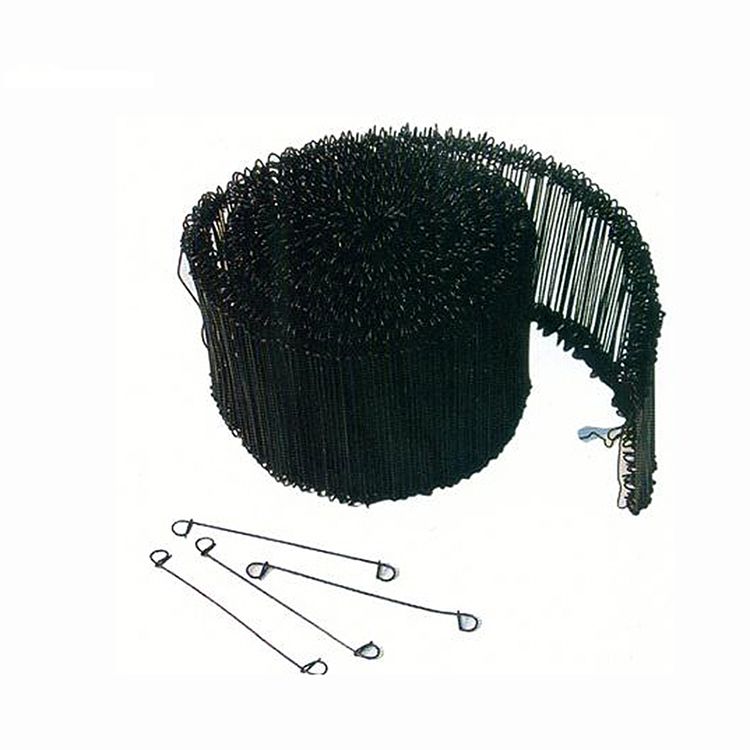
Double Loop Tie Wire
Double loop tie wire material Product Information: Wire diam. 0.5mm—2.0mm Finishes Black Annealed. Galvanized Annealed, Coppered, PVC coated, Stainless steel Wire gauge BWG6 […]
Post time: 2023-06-28