When wiring electricity, there has been much dispute over whether or not you should intertwine the leads before using a wire nut. Both strategies have merits and demerits so it’s helpful to be aware of the contrasts between them before picking an approach.
By knotting the wires prior to using wire nuts, a reliable connection is created for greater security. This offers an extra safeguard against the wires becoming untethered, especially when working with electricity of higher voltage. Without such caution, unfastened wires could result in an unintentional shock or hazardous fire.
Tying the wires together too tightly before using a wire nut can lead to an unsafe electric situation; when the wires are left too tight, they can cause the wire nut to become loose and the connection weak. Unfortunately, this weakened connection is a potential fire risk or shock hazard – one best avoided.
Rather than using a wire nut, if you decide to tie the wires together, severing the connection can be a laborious task. Instead of simply unscrewing the nut, you must painstakingly detach the knotted wires. Therefore, if you anticipate the need to change or fine-tune the wiring in the future, it would be wise to rely on a wire nut for a simpler and swifter disconnection.
Regarding the question of whether to bind wires before fastening them with a wire nut, it really depends on the circumstances. If you’re dealing with electric currents of high voltage, then winding the wires together prior to usage is a smart approach. This not only guarantees a secure section, but it also safeguards against potential fire or electrocution hazards.
If you want a simpler way of connecting low-voltage wiring such as a home alarm system, you may find it more useful to go with the wire nut option. This will help to stay one step ahead in case any repair or other adjustments become necessary in the future.
No matter the internal equipment you’re working with, it’s paramount to always guarantee that the wires are firmly connected before capping them with a wire nut. This implies that extra attention is needed when stripping down the wires and that their ends should remain in impeccable condition. Otherwise, the relationship between them won’t be protected and could result in an unforeseen electrical spark or serious fire.
To ensure the safety of any wiring job, it can make all the difference to understand when to tie wires together before using a wire nut – and when it’s a better option to forgo the process. Generally speaking, tying wires is suggested unless the wires are already in an organized bundle with no need for extra security. Stripping off insulation material and making sure all exposed ends are immaculate are crucial steps to follow for a secure connection that put your safety above all else. By foregoing this safety protocol, you may be leaving yourself open to the risk of an electric shock or fire.
When it comes to electrical wiring work, wire nuts are an essential component that can’t be overlooked. They enable two or more wires to be joined together firmly and securely. Knowing the right time and way to make use of them is a must for completing a wiring job properly. Prior to utilizing a wire nut, you must first ascertain whether or not connecting the wires is necessary.
Nipping wires with a wire nut? Many times, pre-tying the wires is such a helpful strategy! Firmly binding the multiples together prevents slipping and shifting while installing, as this can be hazardous to the insulation and lead to faulty wiring. The additional step ensures that everything stays in place.
Ensuring your wires are secure is key, and the right type of tie is essential for that. Electrical tape should be avoided as it can result in an undesirable short circuit when wires become loosed. A twist-on connector or plastic zip tie would be much more reliable and effective; these ties are manufactured to lock wires in place and make sure they remain securely attached.
After the wires have been intertwined, the wire nut is the perfect way to seal the joint securely. Before installing the wire nut, carefully survey the wires to ensure that all edges are neatly bonded and not frayed. If any roughness is present, snip off that section before affixing the wire nut.
To fit the wire nut snugly, firmly press down on it until it is firmly fastened to the wires. After this step, take a moment to check the spot where the wires join – no gaps or revealed wires should be present. This way, you can rest assured that the wire nut will stay locked in place.
Before using a wire nut, it is advisable to tie the wires together so that they remain securely anchored. Doing this will stop them from shifting within the nut during installation, as this can disrupt the insulated covering of the cable and cause a potential short-circuit. Despite its simplicity, this connection process should not be taken lightly – it has the power to safeguard your wires.
It is imperative to choose the correct tie when uniting electrical wires. Twist-on connectors or plastic zip ties should be utilized, as electrical tape has the potential to generate a dangerous short circuit in the event of jostling wires. These ties are fabricated specifically to preserve steady wire positioning and prevent them from staggering.
To guarantee your wiring goes off without any inconveniences, try using these steps. Securing the wires in place before grabbing the wire nut is the ideal approach to keep you from making any costly mistakes and guaranteeing that your wiring is properly done.
Related Product
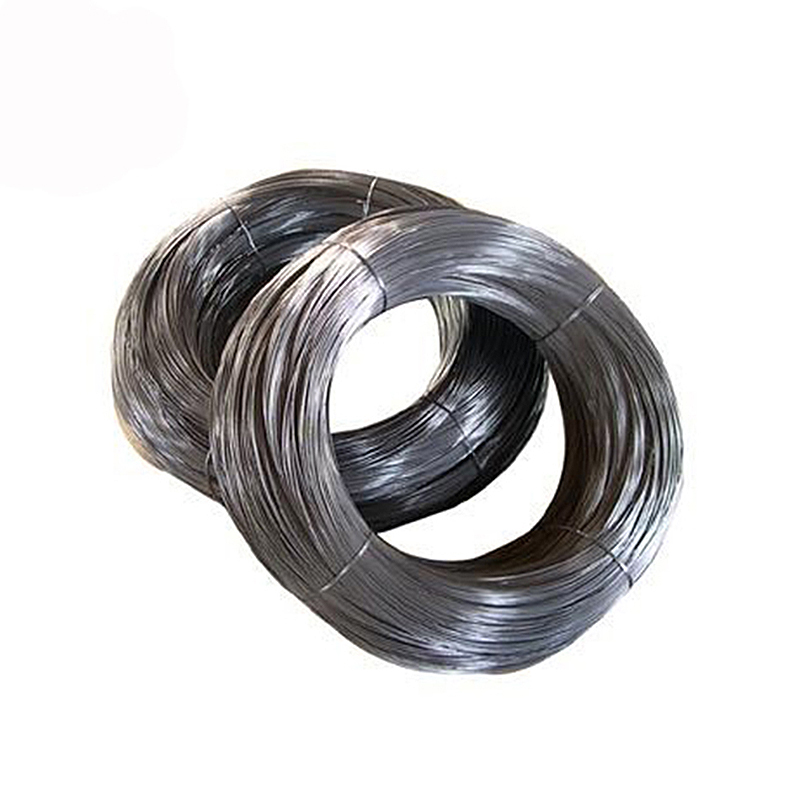
Galvanized Wire
Product information: Product Name Galvanized Wire Package 5kgs/roll, pp film inside and hassian cloth outside or pp woven bag outside 25kgs/roll, pp film inside and hassian […]
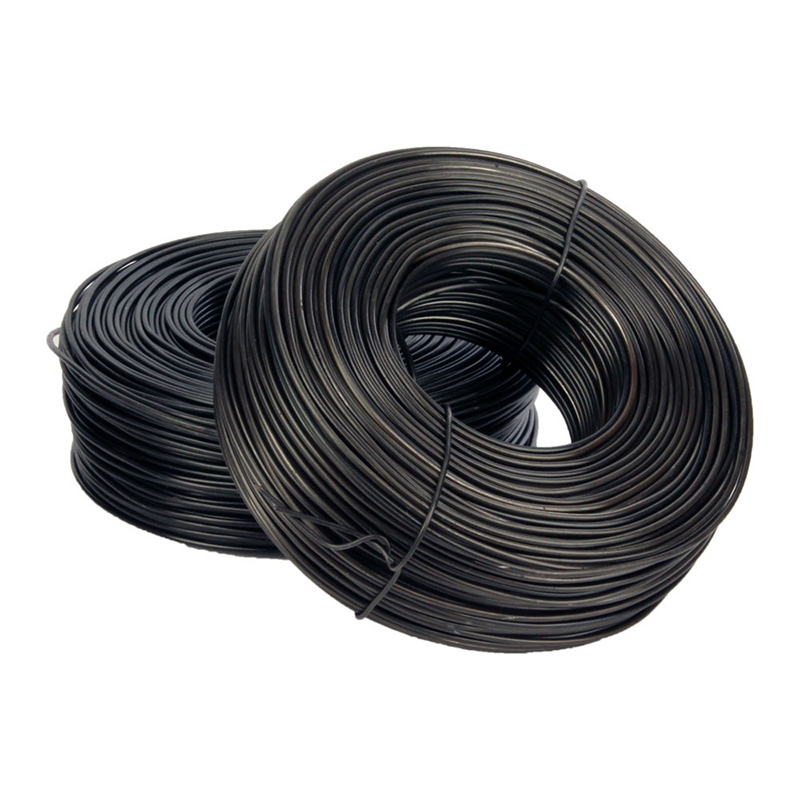
Tie Wire
Production Process of rebar tie wire : Steel rod coil — Wire Drawing — Wire Annealing–Rust Removing–Acid Washing– Boiling– Drying– Zinc Feeding– Wire Coiling. Wires Type 1.Galvaniz […]
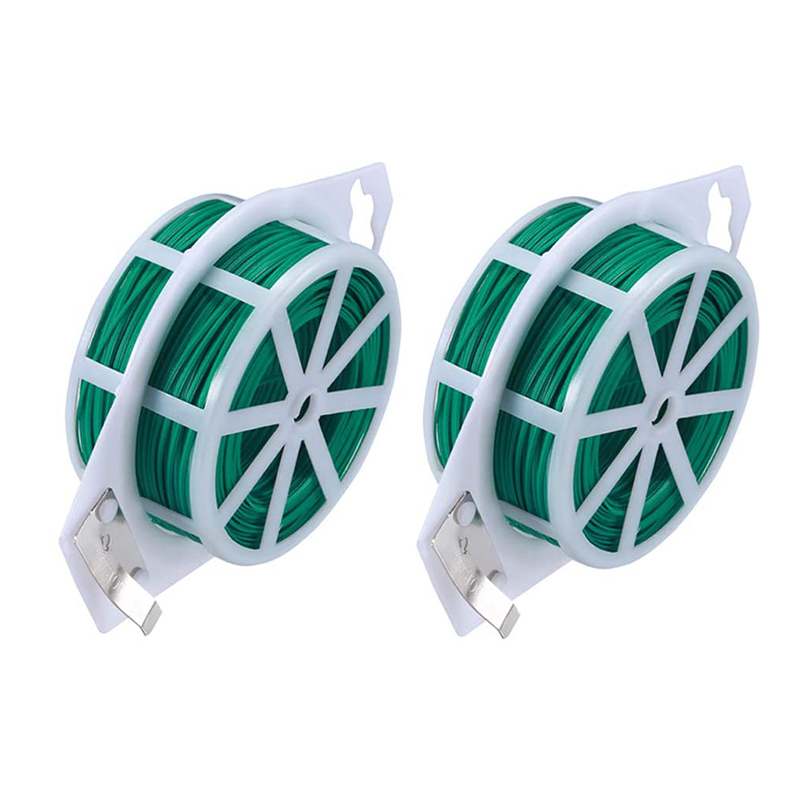
Garden Wire
Product information: The garden shingling is made of pvc plastic and high-quality galvanized iron wire, which is 3 to 4 times faster than any material, and the buckle is loose, the […]
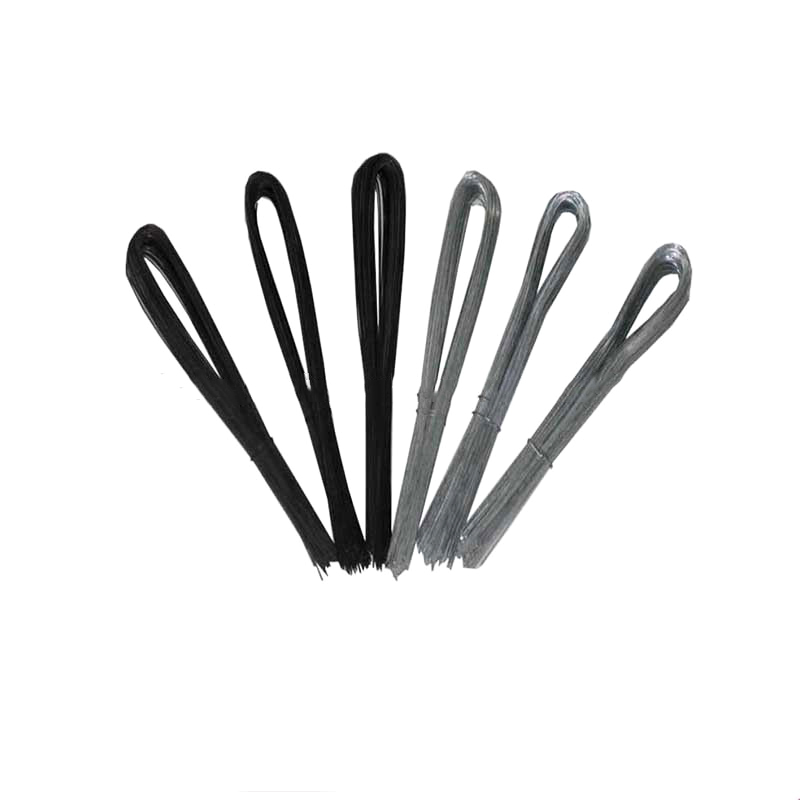
U Type Wire
Product information: Product Name Scaffolding Packing Galvanized Tie Wire Cuttings U Type Binding Wire Material Electro galvanized,hot dipped galvanized,black annealed,PVC coated W […]
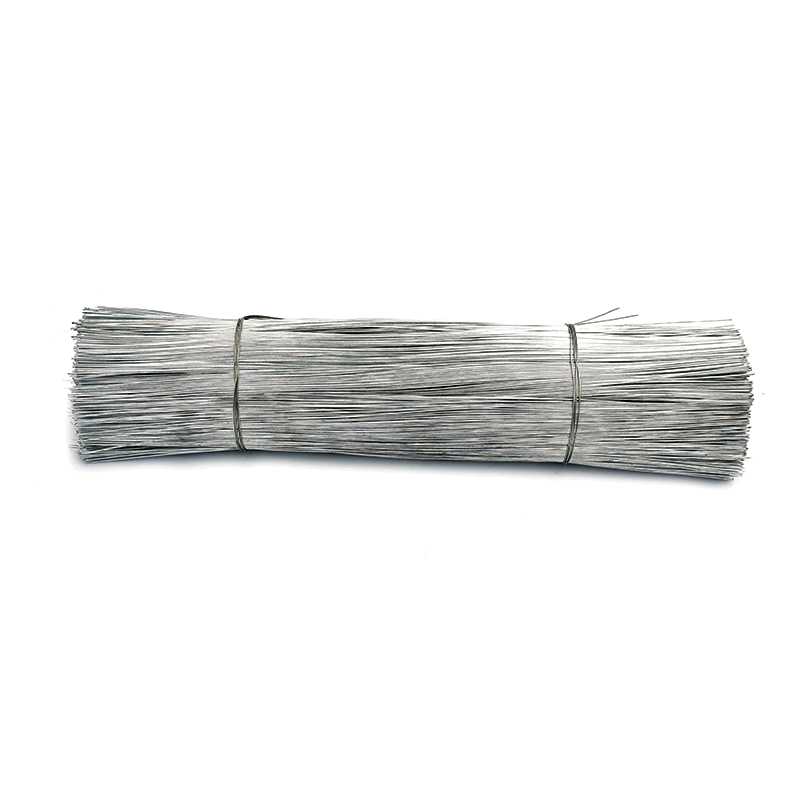
Cutting Wire
Product Description: Product Name Cutting Wire Zinc Coating 30-70g Place of Origin Chinese mainland Tensile Strength 33-50kg/mm2 Material Electro galvanizedHot dipped galvan […]
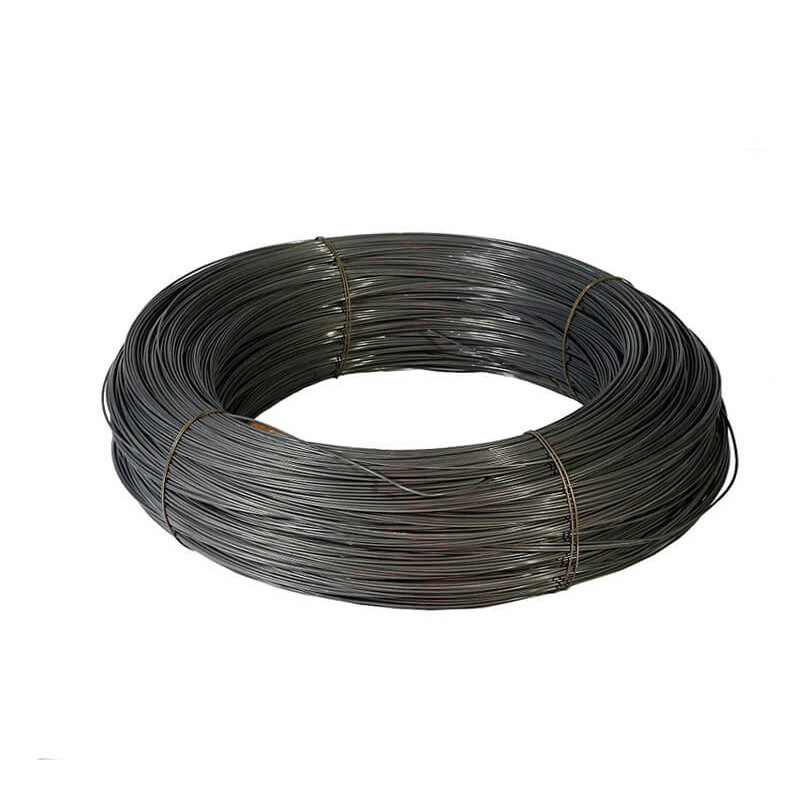
Black Annealed Wire
Product Description: Product name Black Annealed Wire MOQ: No Material Q195,Q235 Delivery time: 20days after payment Surface annealed or as your request Payment terms: T/T,L/C We […]
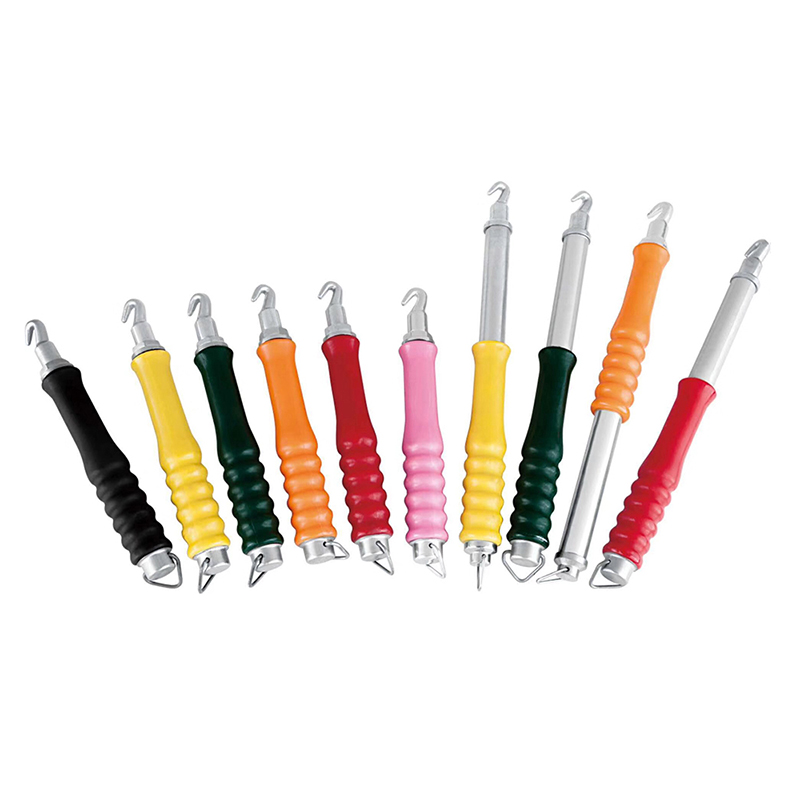
Twister Tool
Handle Twister tool,plastic handle: Weight: 0.4kg Color: Black, blue,yellow ,red etc Material: Carbon Steel Plastic Handle Wire Tie / Tying Hook Tool Twister Wooden Handle […]
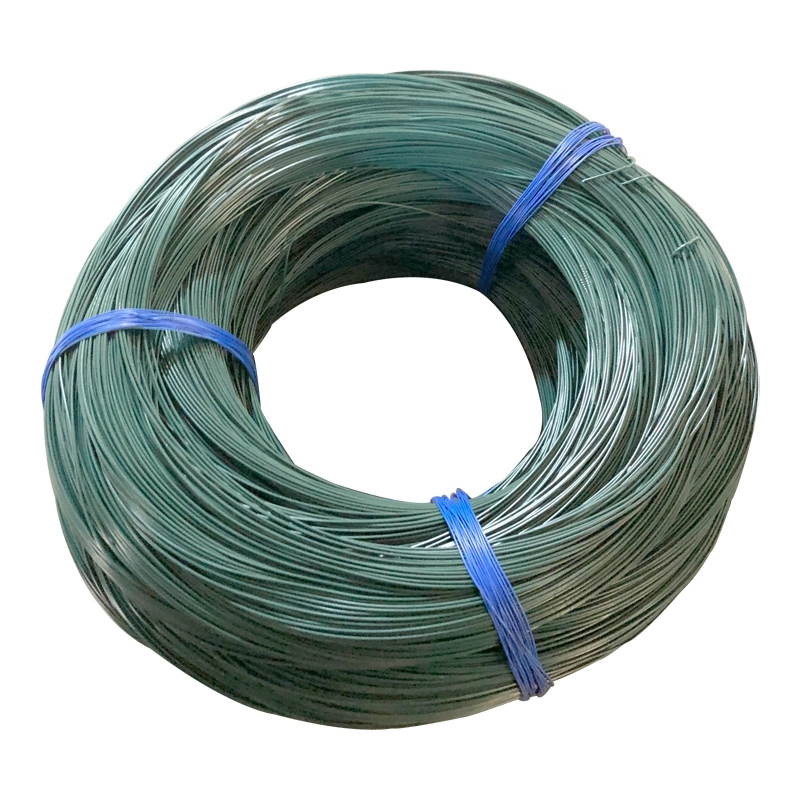
PVC Coated Wire
PVC coated wire, also called plastic coated wire, after high temperature dissolution cooled solid PVC particles uniformly wrapped in high-quality black iron wire and galvanized wi […]
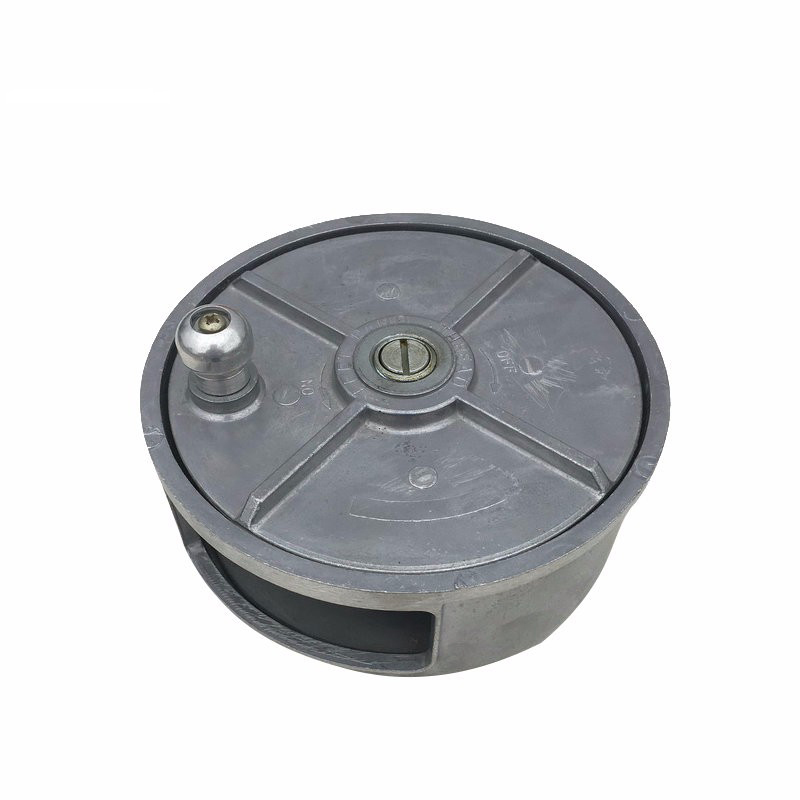
Reel Wire Tool
Product information: Specification of Aluminum Tie Wire Reel Material Plastic & Aluminum Weight 1.95LBS Application Binding Wire MOQ 1000pcs Sample Free Package 5PCS/CARTON &nb […]
Post time: 2023-08-07